To the limits of cold forming.
The companies of the ESKA Group share the common core competence of massive cold forming and thus the manufacture of high-strength metal products with a high degree of forming. For 140 years, the limits of forming technology have been constantly redefined for the benefit of customers. Today, 403 employees at two German sites develop and produce fasteners and formed parts.
The technological basis is the multi-stage press with four to six forming stages. Our customers value the innovative products, excellent quality and perfect logistics of the ESKA brand. It has made our company a recognized development partner.
Reliability
Our roots lie in the automotive industry and have taught us to meet the highest standards. Our management systems and certifications are our references for quality and excellence. We now bring this know-how to various industries. In addition to our strong foundation, we have a powerful network to fall back
Our service
As a development service provider with our own tool shop, we are the perfect combination of flexibility and expertise. We are not only developers, but also problem solvers. Our aim is to tackle your fastening problem efficiently and innovatively. With our versatile skills and modern toolmaking facilities, we can develop customized solutions for your requirements.
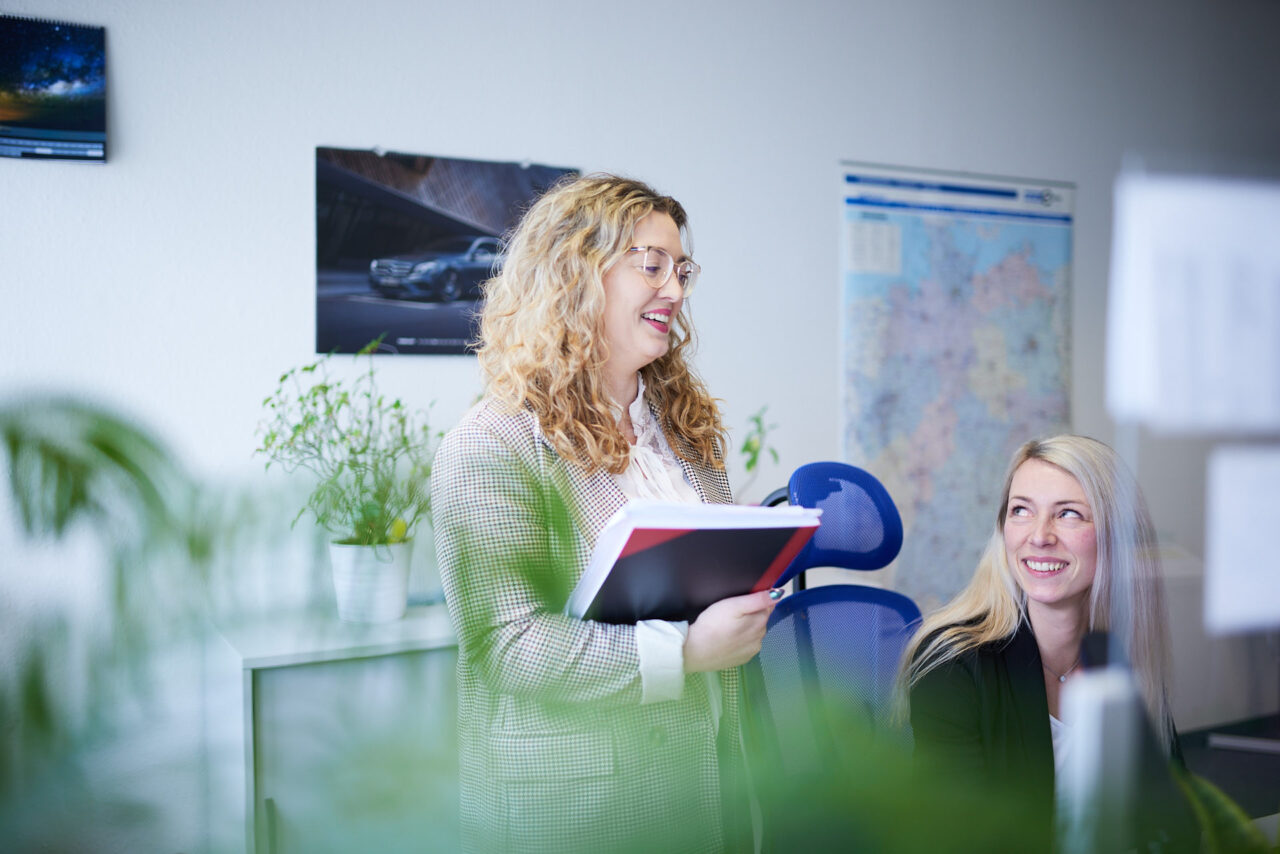
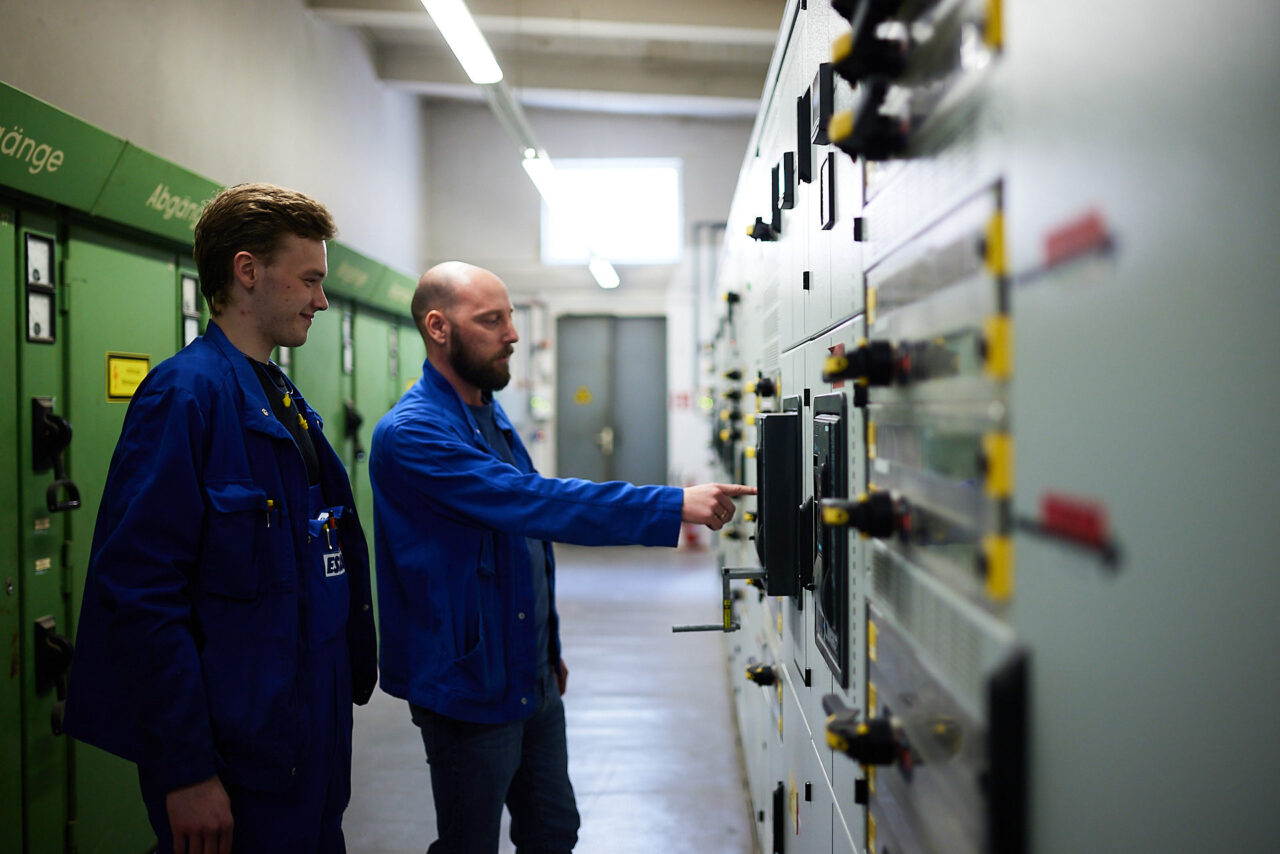
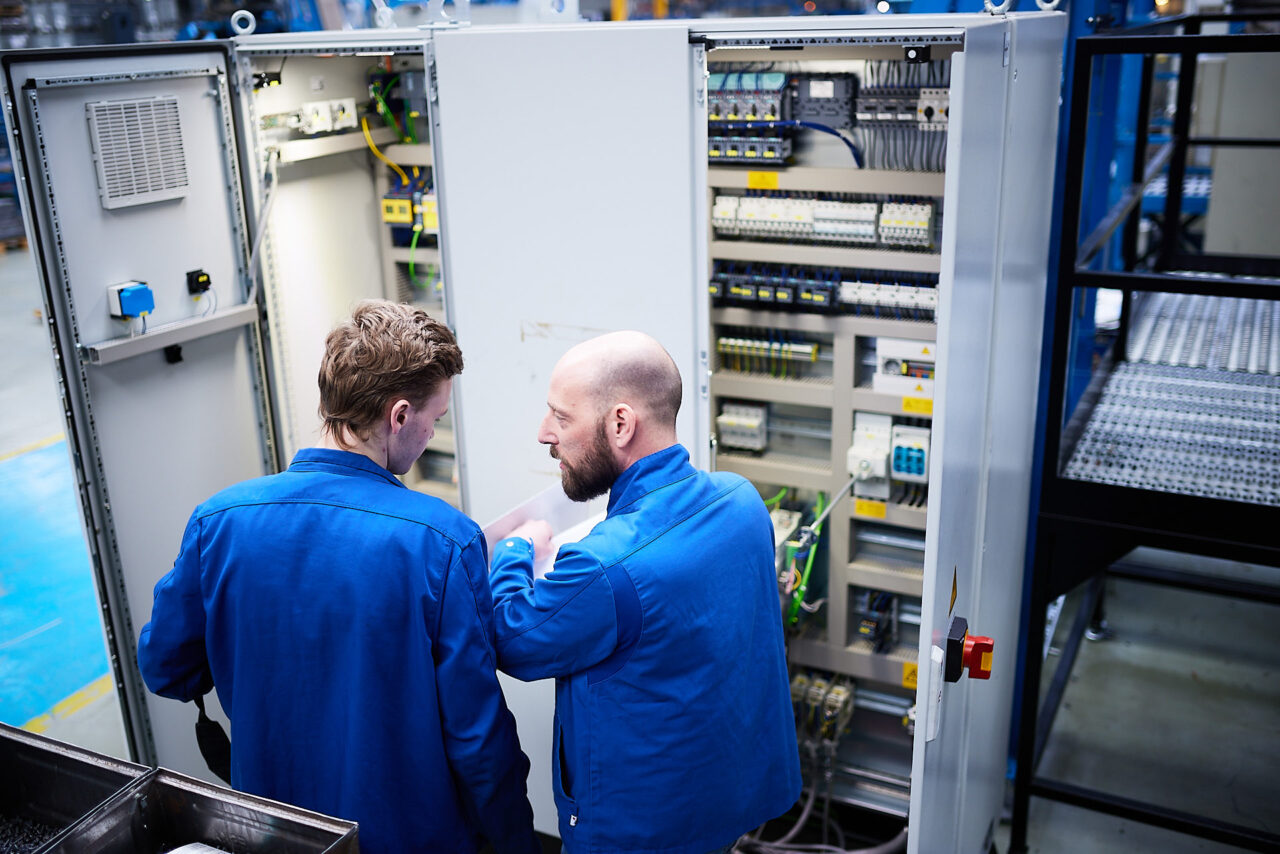
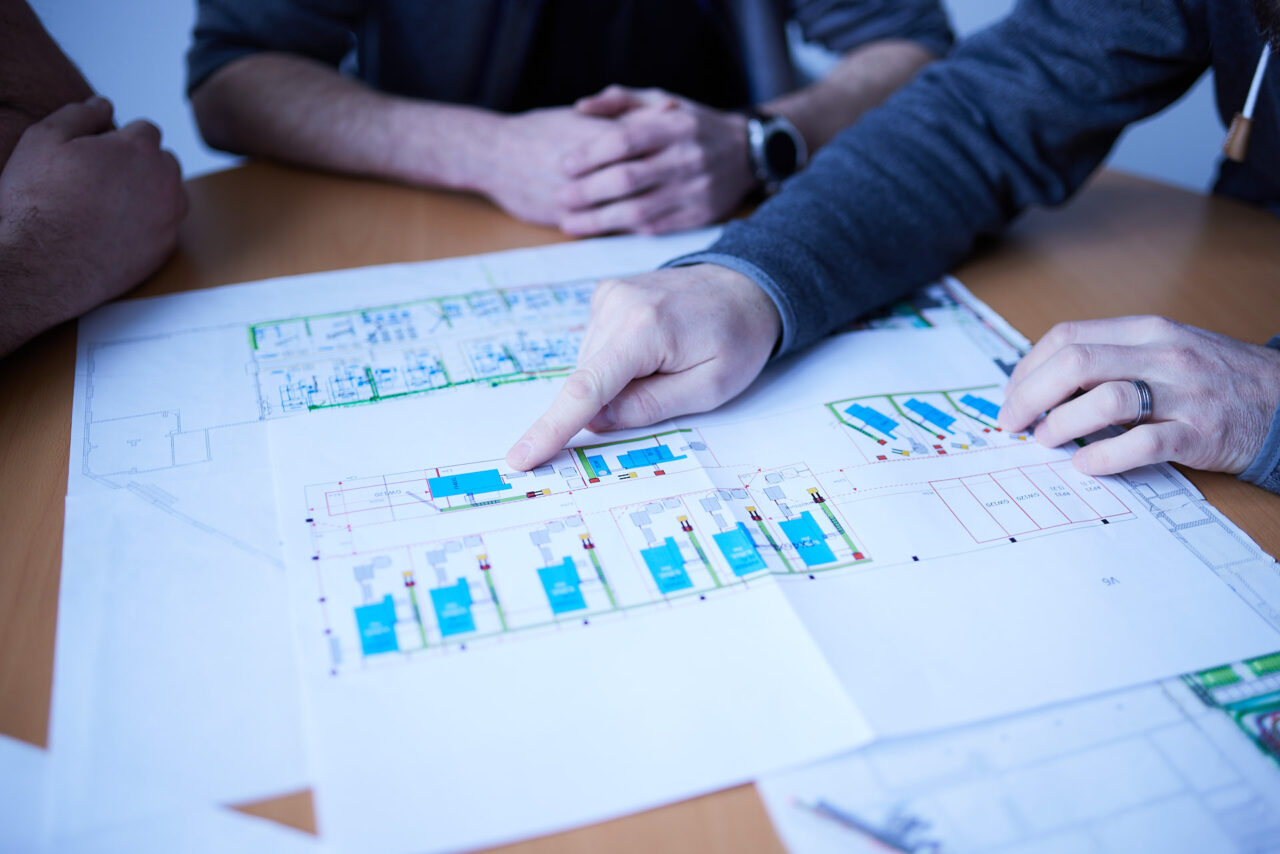
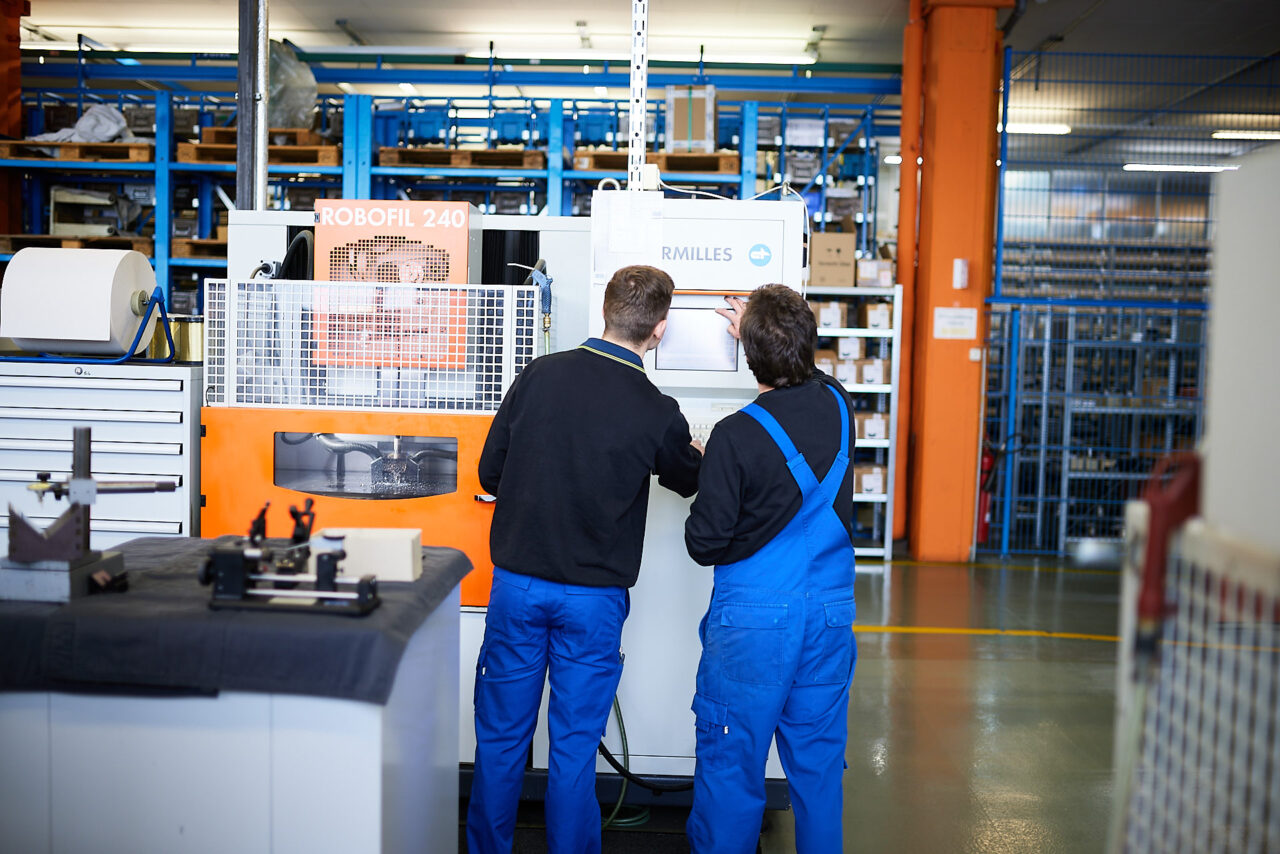
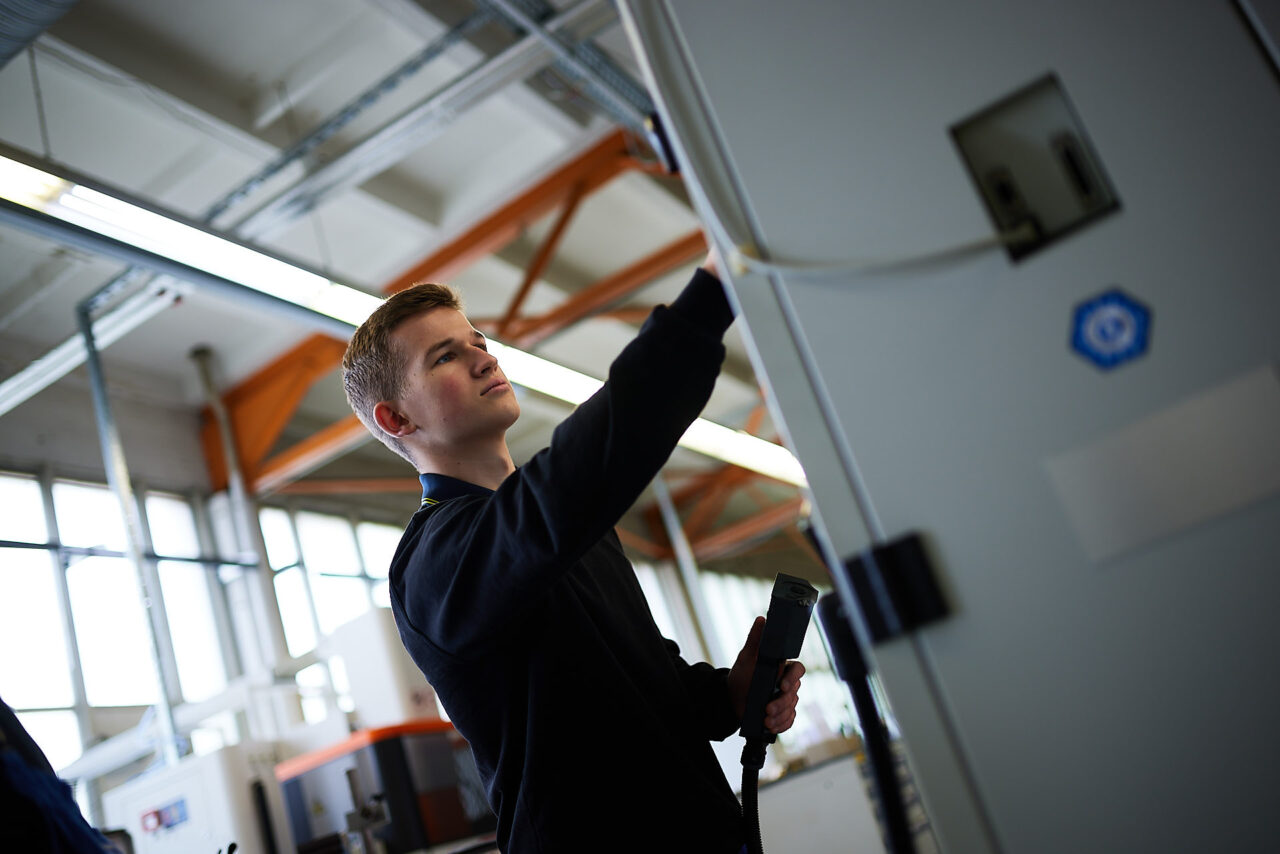
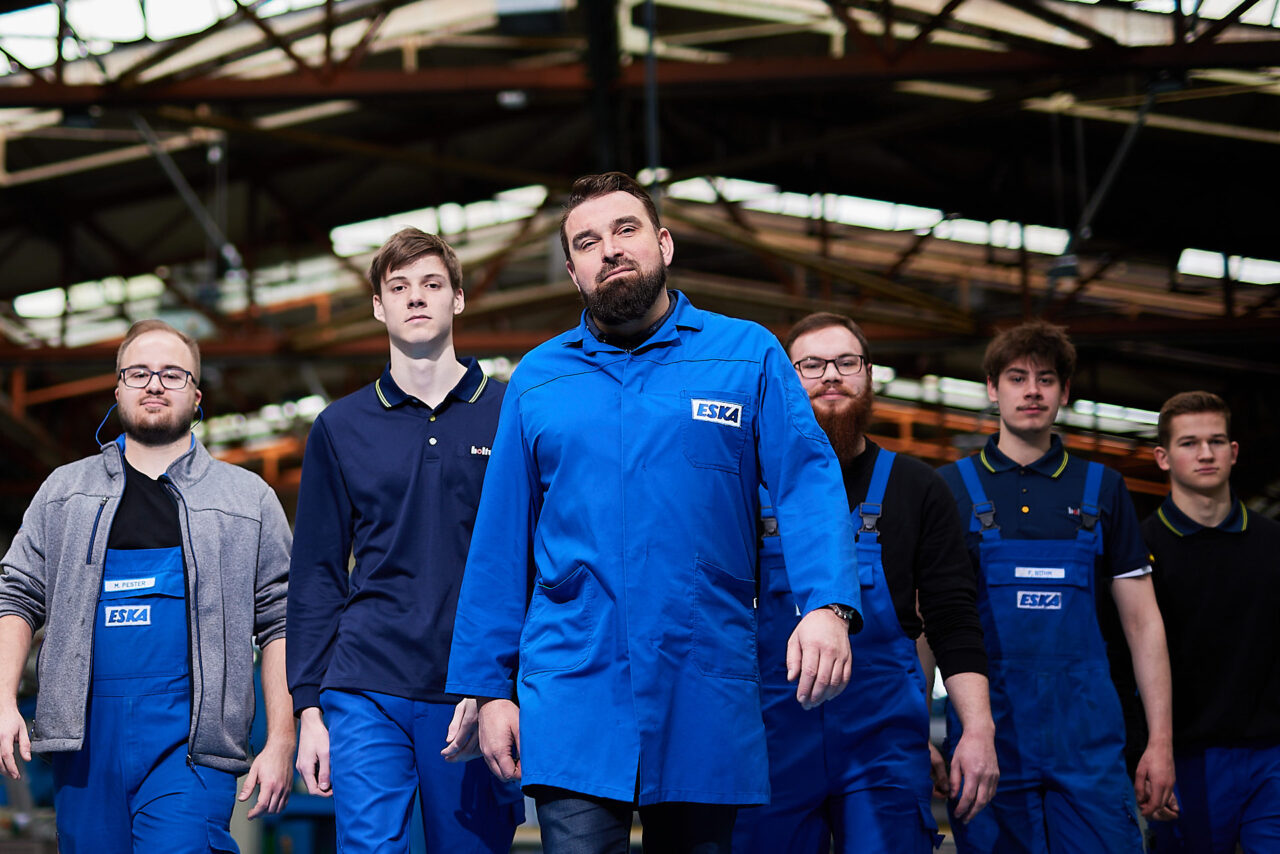
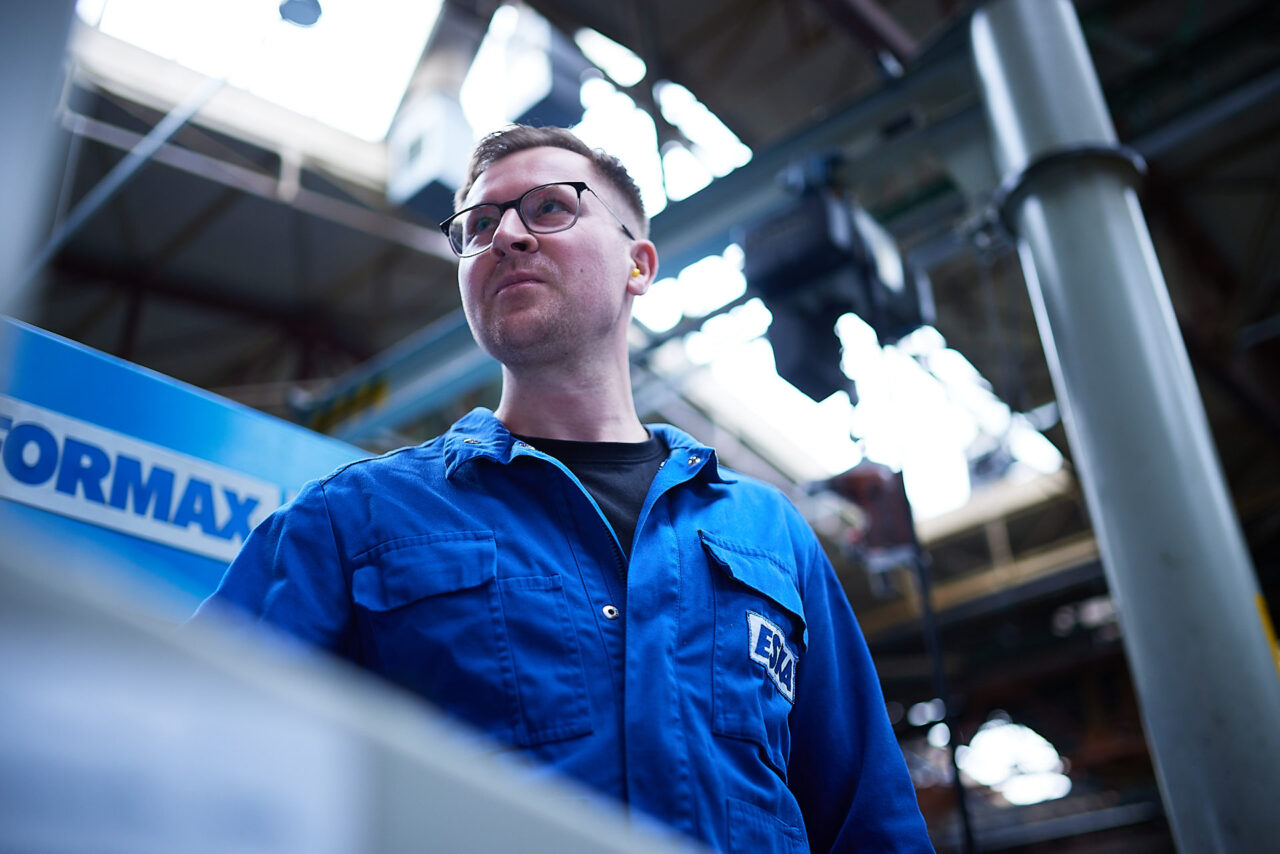
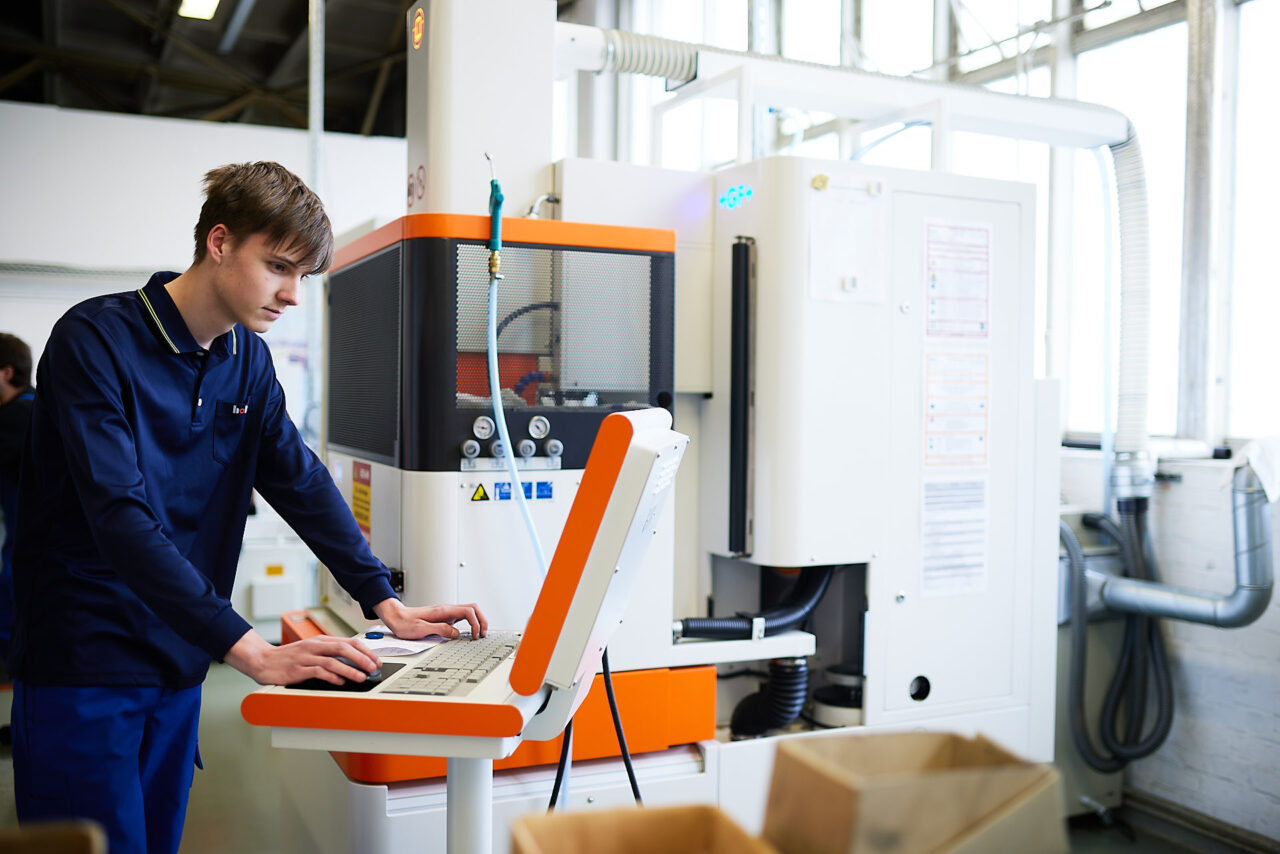
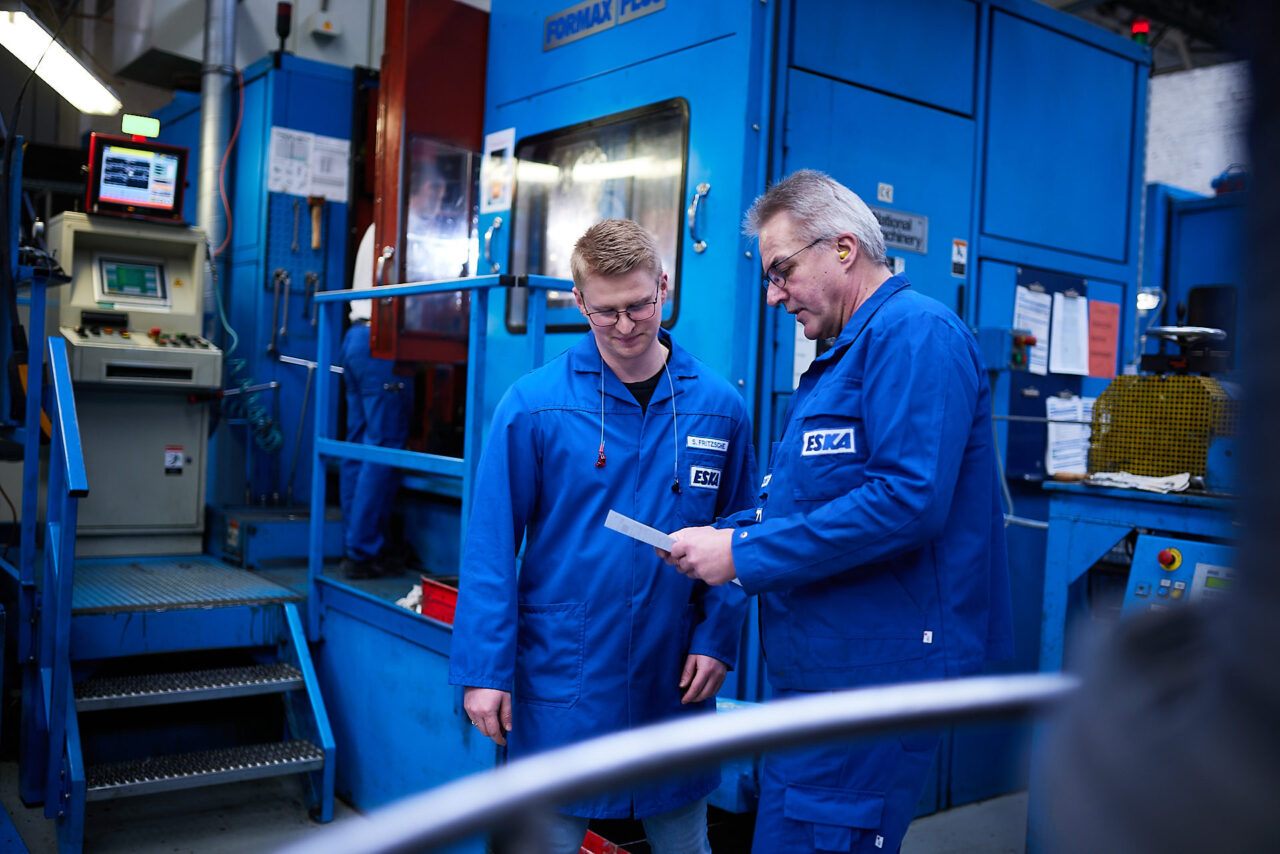
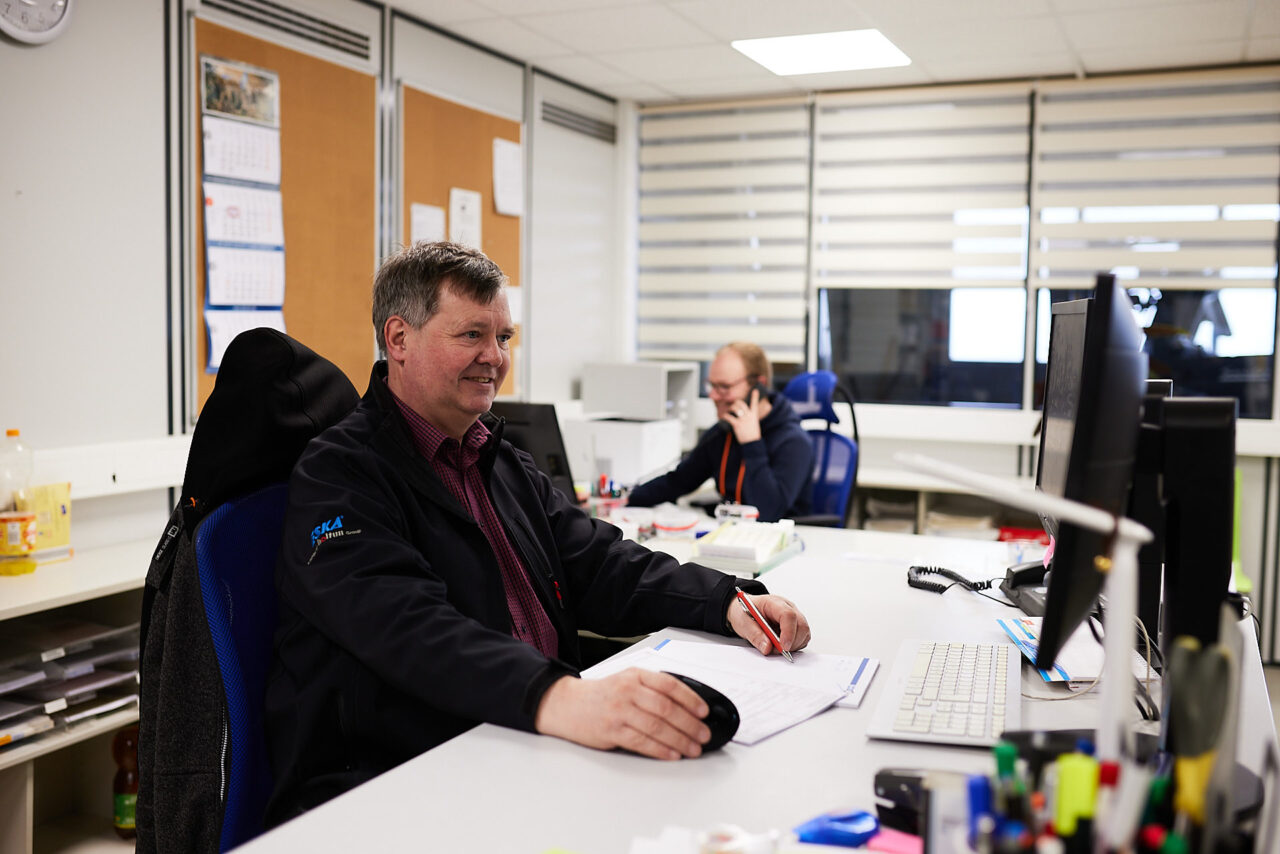
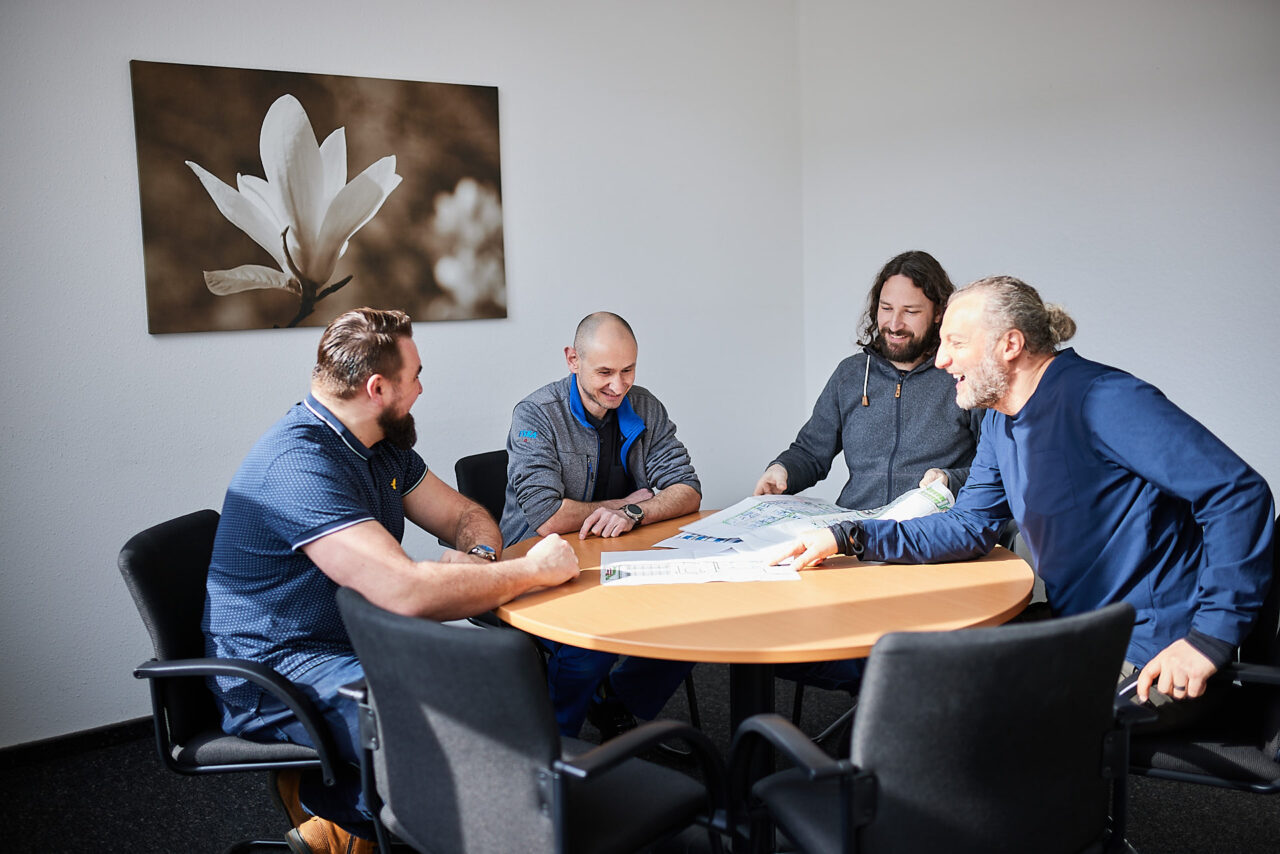
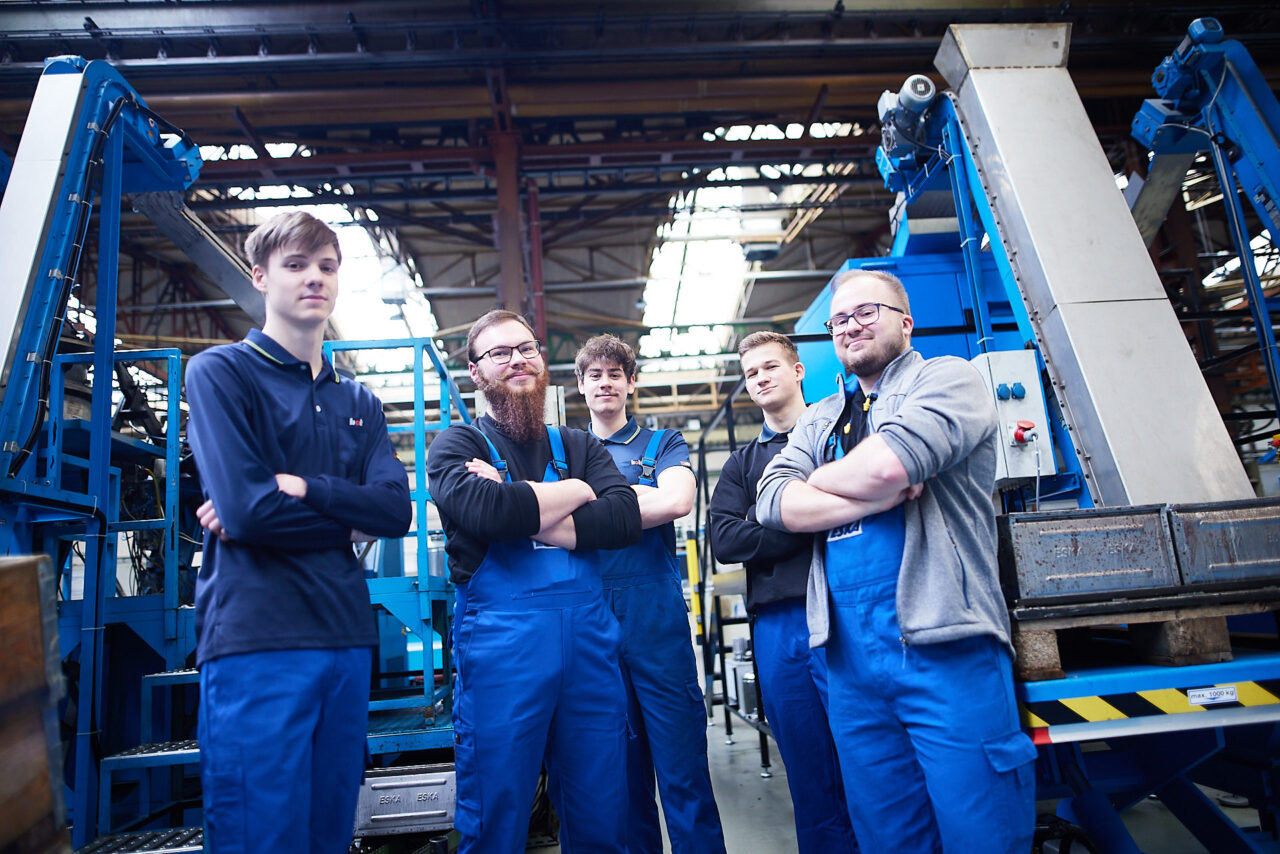
Locations
ESKA Automotive GmbH
Lutherstraße 87
09126 Chemnitz
Germany
Telefon: +49 371 5705-0
Telefax: +49 371 5705-319
ESKA Automotive GmbH
Umformwerk Bärenstein
Oberwiesenthaler Straße 23
09471 Bärenstein
Germany
Telefon: +49 37347 185-0
Telefax: +49 37347 185-30
ESKA Automotive Logistik Zentrum
Blankenburgstraße 81
09114 Chemnitz
Germany
ESKA China
Xiamen ESKA Automotive Co.,Ltd.
Part two of No.2 Plant,No.666,Tonghui Road,Tongan
District, Xiamen
China
Facts
403
Employees
4
Locations
85
million € turnover p.a.
16
thousand tons Annual capacity
37
million € Investment
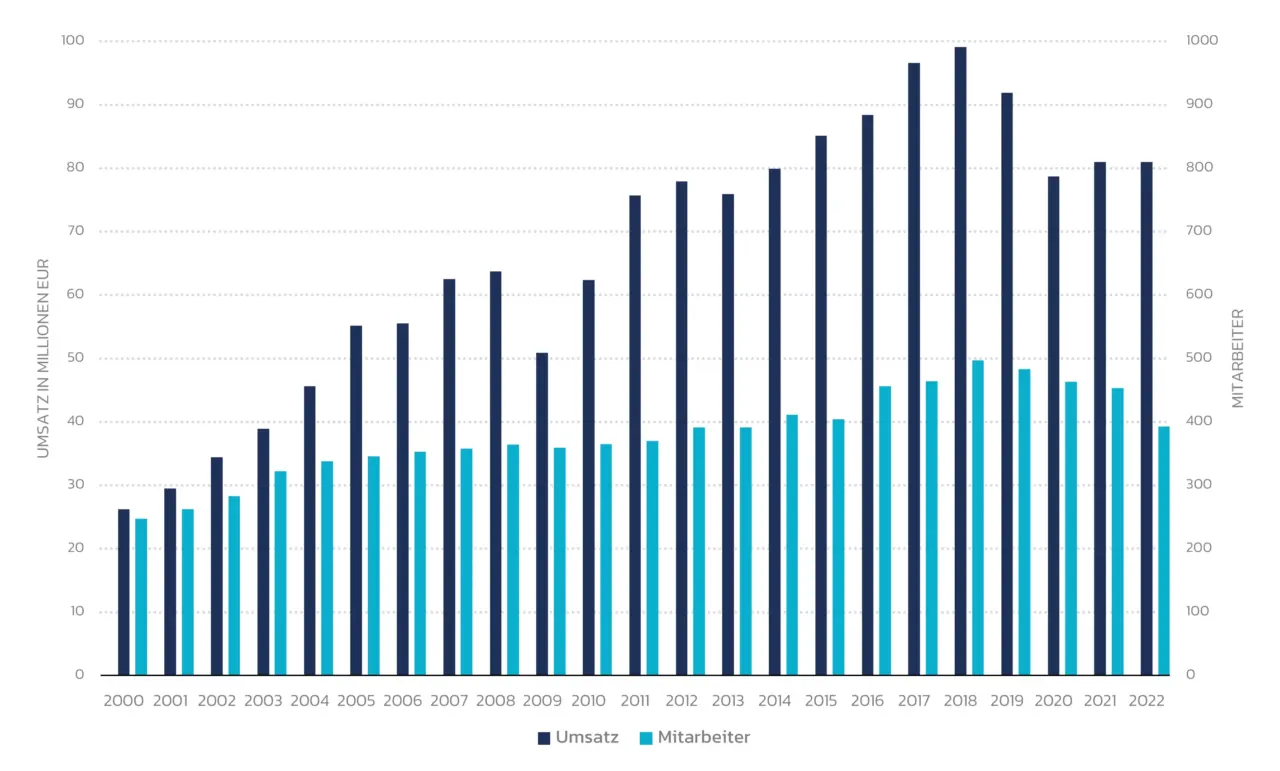
History
1881
Foundation of the company
The history of today’s ESKA group of companies goes back to the founding year 1881, when industrial mass production of screws and nuts began at the same location in Chemnitz under the company name Sächsische Schrauben und Muttern – Fabrik (Saxon Screws and Nuts Factory), even before the invention of the automobile.
The company subsequently developed very successfully, also by expanding its core competence at the time by taking up activities in its own mechanical engineering for wire processing and forming, and held patents in this sector in all industrialized countries.
As early as 1930, the company’s previous legal form was changed to that of a stock corporation in order to meet the capital requirements for further growth in all business areas.
The company, now operating under the name Archimedes AG, was one of the most important German producers during this period with very considerable export quotas.
1945
Total destruction and reconstruction
In March 1945, Chemnitz, once one of the richest industrial cities in Germany, was totally destroyed by Allied air raids. At the same time, 225 factories were completely destroyed or shut down for a long time. Archimedes AG also suffered this fate.
1984
Kombinat Wälzlager und Normteile with 3,030 employees
After the division of Germany, reconstruction and the gradual start of production began under the now centralized state system. Monopolistic economic structures led to more than 3,000 employees by 1984, with five further parts of the Chemnitz site, and once again to a high level of recognition.
After the reunification of the two German republics, Sächsische Schraubenwerke, like all other large monopolistic companies, had to undergo a far-reaching adjustment process.
Misjudgements of future market developments meant that attempts by foreign investors to continue the majority of previous production sites under market economy conditions failed immediately after reunification. Market forces set insurmountable limits.
Even before the turn of the millennium, both production sites were among the group of companies that helped to write the success story in Saxony after completing restructuring and successfully entering the market.
1993
Privatization to K. Gruber and W. Stoffel with 115 employees
At the end of 1993, the then shareholders, Klaus Gruber and Winfrid P. Stoffel, took over responsibility for the Chemnitz site. With a new conceptual focus on the automotive target groups and their quality requirements, considerable new investments were made alongside the necessary total product change.
1995
Takeover of Schraubenwerk Bärenstein with 35 employees
In 1995, Klaus Gruber and Winfrid P. Stoffel also took over responsibility for Schraubenwerk Bärenstein GmbH, thus further expanding the product range in terms of breadth and capacity.
2006
125th company anniversary
With the 125th company anniversary in 2006, the company operates under the company name ESKA Automotive.
2014
Sale to the Boltun Group based in Taiwan
Since August 2014, ESKA has been fully owned by the Boltun Group, Boltun Europe Holdings GmbH & Co. KG
2016
New aluminum center
2017
New ESKA logistics center
2018
New production site in China Xiamen ESKA CHINA
Sustainability
Sustainability policy of ESKA Automotive GmbH
ESKA Automotive GmbH is a globally active company with locations in Europe and Asia. We are aware of our responsibility and contribute to the preservation of nature and the environment.
We base our actions on the UN Sustainable Development Goals
Our employees are our company’s top priority. We pay attention to gender equality as early as the personnel planning stage. We increase the qualifications and personal development of our colleagues through ongoing training programs. Safe and healthy workplaces and equipment help to maintain health. We ensure employee satisfaction through fair pay and attractive additional social benefits. The offer of mobile working and flexible part-time and full-time working time models are further building blocks for reconciling family and career. Our German sites are certified to ISO 14001, ISO 45001 and ISO 50001 and are regularly monitored.
Our products make it possible to create detachable connections. Our vision is to enable further use of our components over the life cycle of the application. The reuse of parts saves resources to a considerable extent and takes precedence over product recycling. Sustainability is already taken into account in the design of the parts. The aim is to enable our parts to be used for many years. After use, the parts should be recyclable in order to create a circular economy. The efficient process of cold forming enables the material used to be kept constant in volume from the first forming stage to the finished part.
In contrast to machining, this technology reduces the use of materials to a minimum. In production, we rely on energy-efficient measures to reduce the resources used. Heat recovery and the use of district heating help us to minimize the use of fossil fuels. In future, this will be supplemented by the use of photovoltaics. We are aiming for zero defects in order to increase quality and customer satisfaction and reduce the use of materials. Our employees are actively involved in the CIP process. The development of new technologies increases our expertise and flexibility and enables us to reduce transport routes and resources used through insourcing. Automation and further digitalization support these processes.
ESKA already supplies a large number of parts made of aluminum. The weight advantages of lightweight construction reduce fuel consumption and make it possible to design more filigree supporting structures. We manufacture parts made of copper for the expansion of e-mobility. The material is used in these applications due to its excellent conductivity. We also apply the sustainability requirement to our supply chains for raw materials and contract work. Overall, we enable our customers to achieve their own sustainability goals in the best possible way via the supply chain.