Cold forming
Wire sections are formed under high pressure between a die and a punch. This causes the material to flow and change its shape. If the initial diameter is increased, this is referred to as upsetting. If it is narrowed, it is referred to as reducing or extrusion. The material is brought into the desired final contour in a single operation in up to 6 forming stages without cutting and at high speed. Complex geometries and hollow parts can be produced.
Advantages
- high dimensional accuracy
- high surface quality
- continuous fiber flow through forming
- work hardening
- efficient process for mass production
- material savings compared to machining
- higher dimensional accuracy compared to hot forming
- production on modern horizontal 4- to 6-stage presses
- wire diameters from approx. 5 mm to approx. 35 mm can be processed
- materials: steel, aluminum, copper and other cold-formable materials
- high production speeds (up to 300 pieces/min)
- maximum material utilization
Aluminum center
3,000 m² production area for 2,400 tons of Aludrive® screws per year. State-of-the-art and unique production center for aluminum fasteners.
- 6 multi-stage presses for cold forming
- two furnace lines including drum washing machines
- 6 thread rolling machines
- fully automatic parts transport with driverless transport system
- fully automated small parts warehouse for more than 3,000 containers
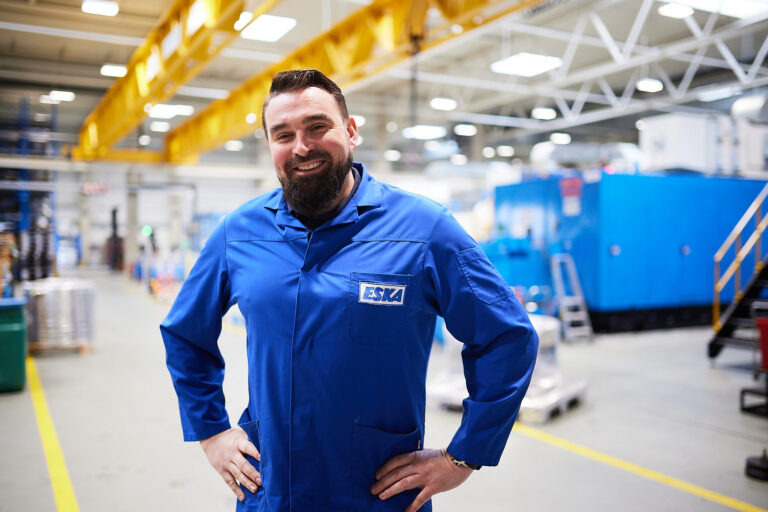
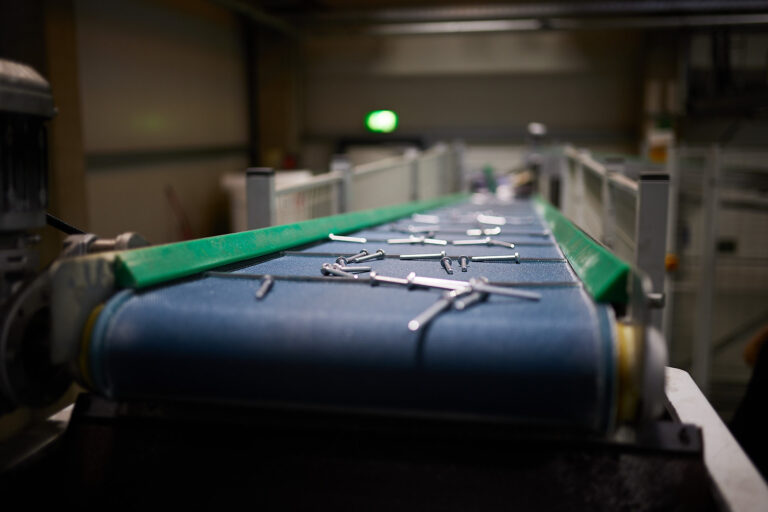
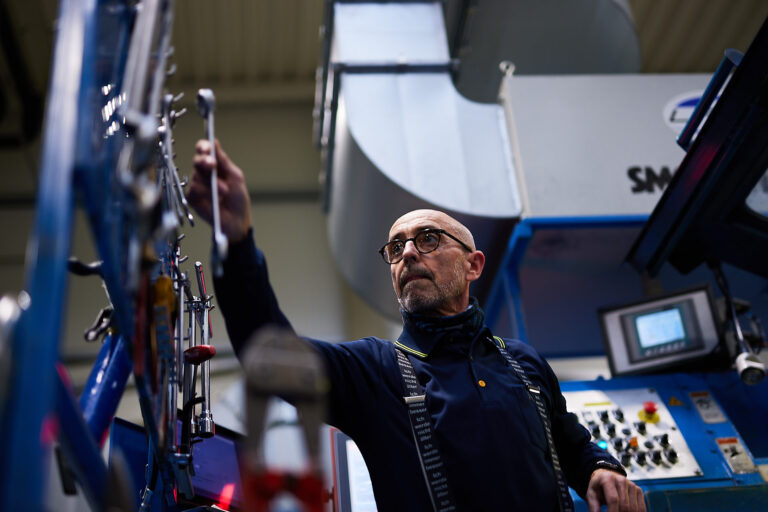
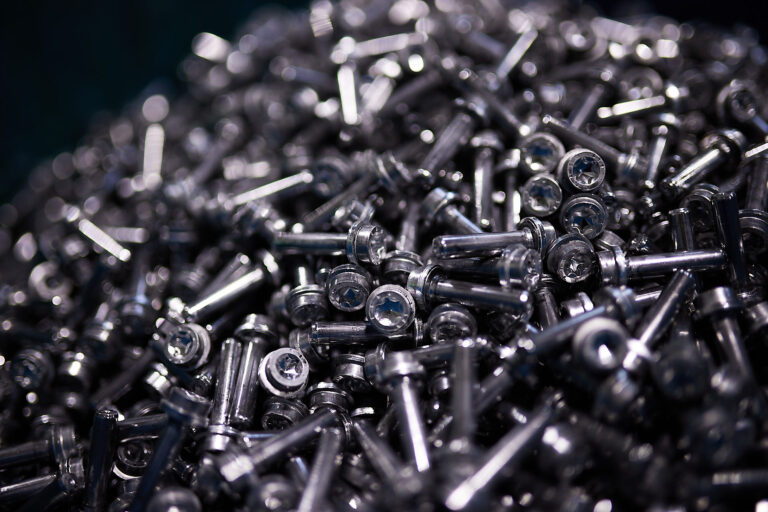
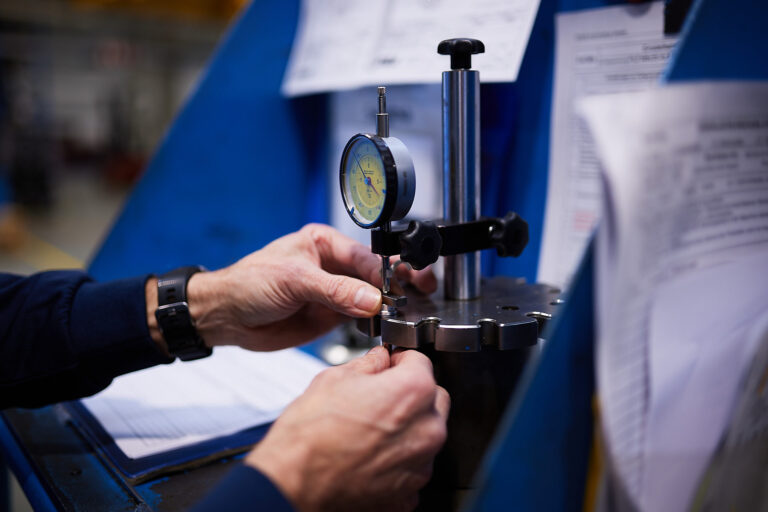
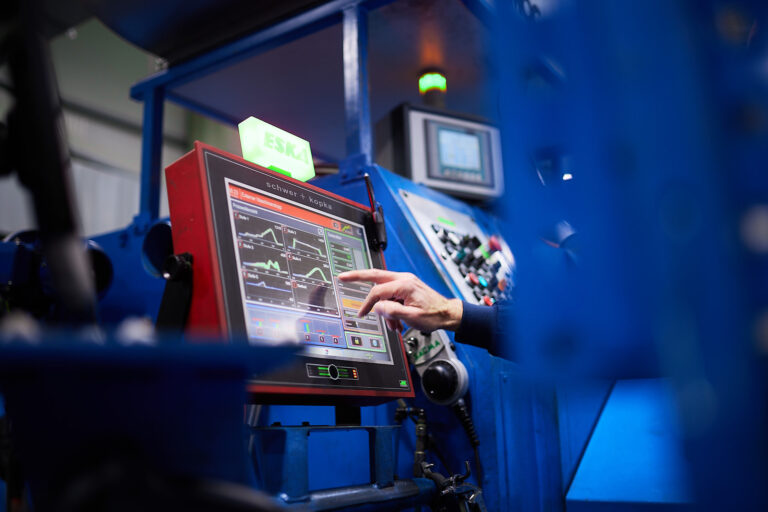
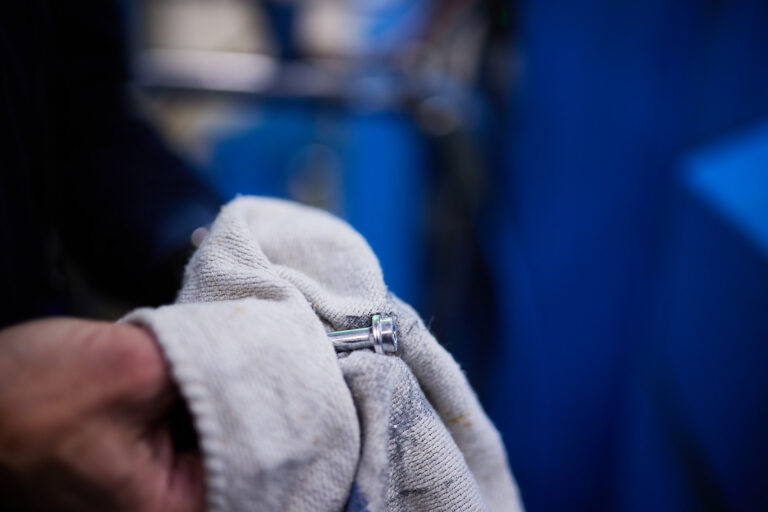
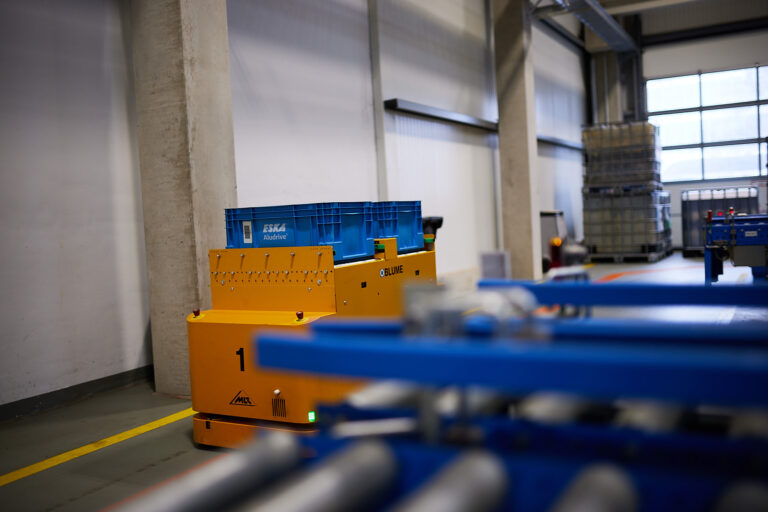
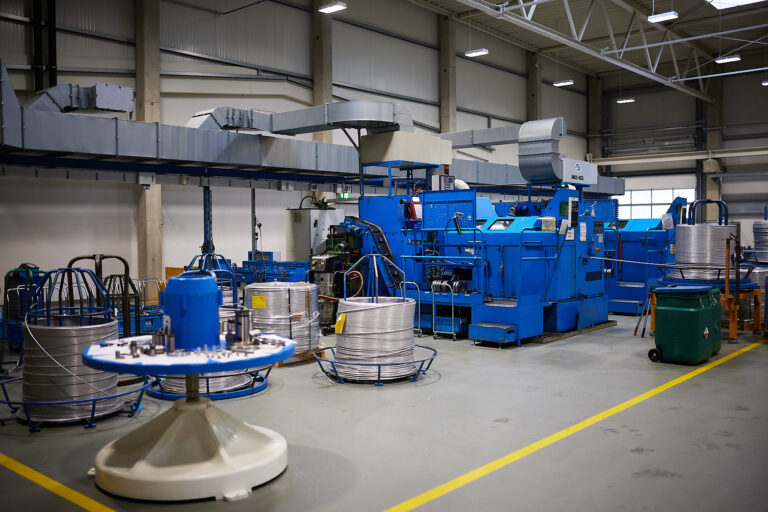
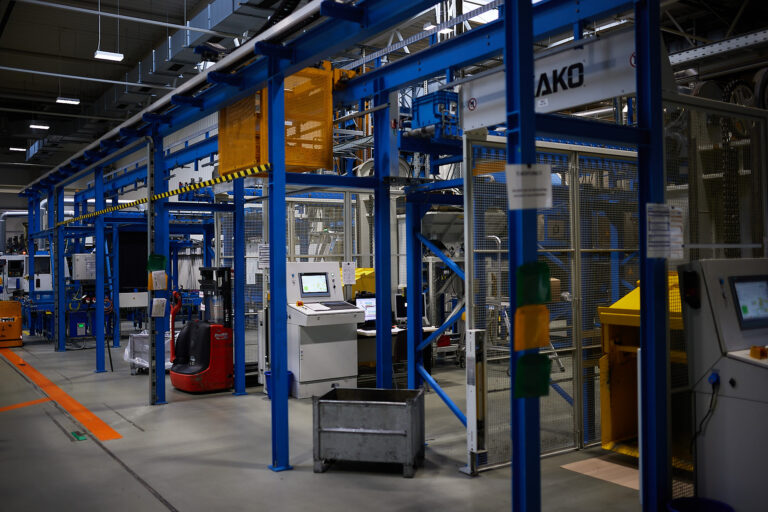
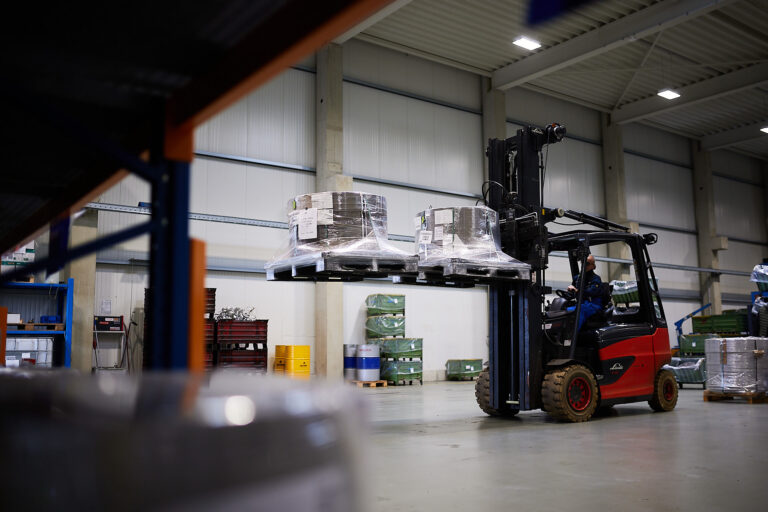
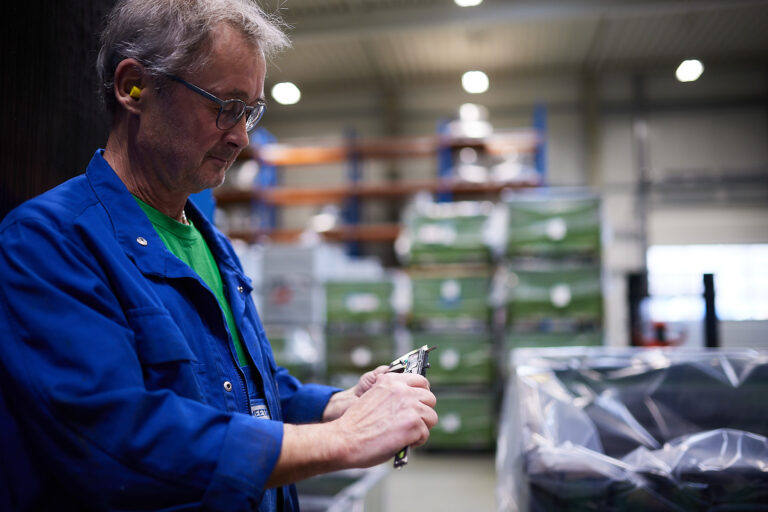
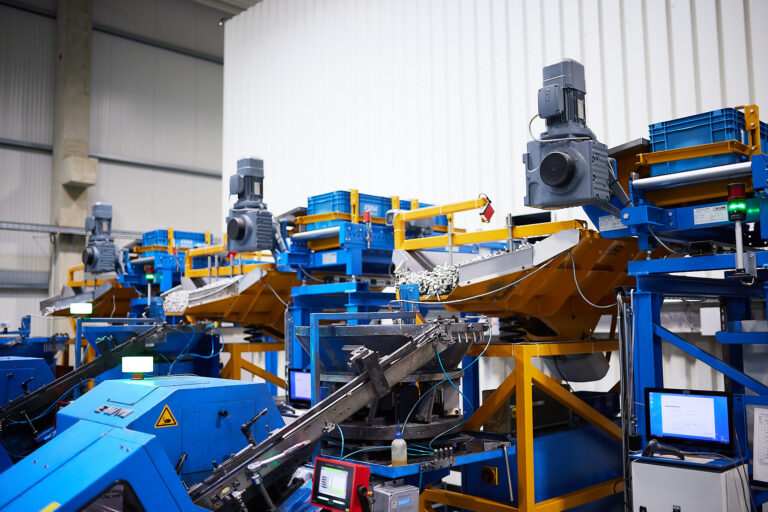
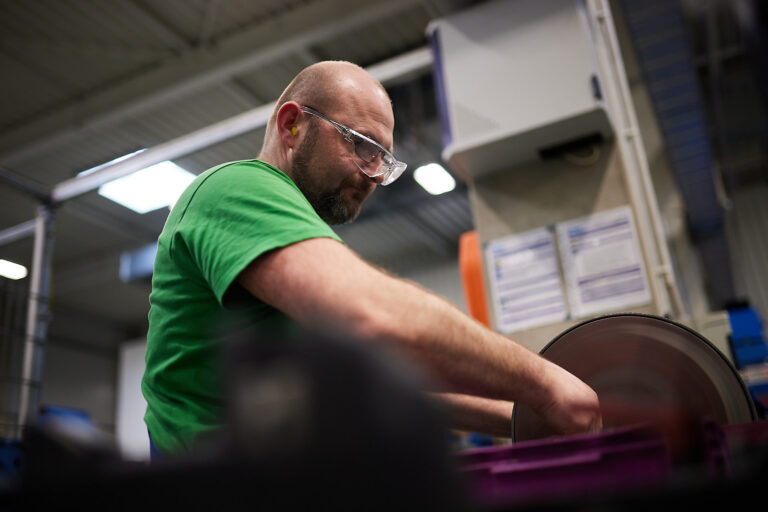
Tempering / heat treatment
Process:
- quenching and tempering of steel in strength classes 8.8 to 12.9 and higher
- precipitation hardening of aluminum alloys
The applications for ESKA products generally place special demands on material strength. ESKA specializes in high-strength fasteners and formed parts. The heat treatment of the products to achieve specific strengths is carried out in-house using two heat treatment lines each for steel and aluminum materials. All parameters are strictly monitored and recorded.
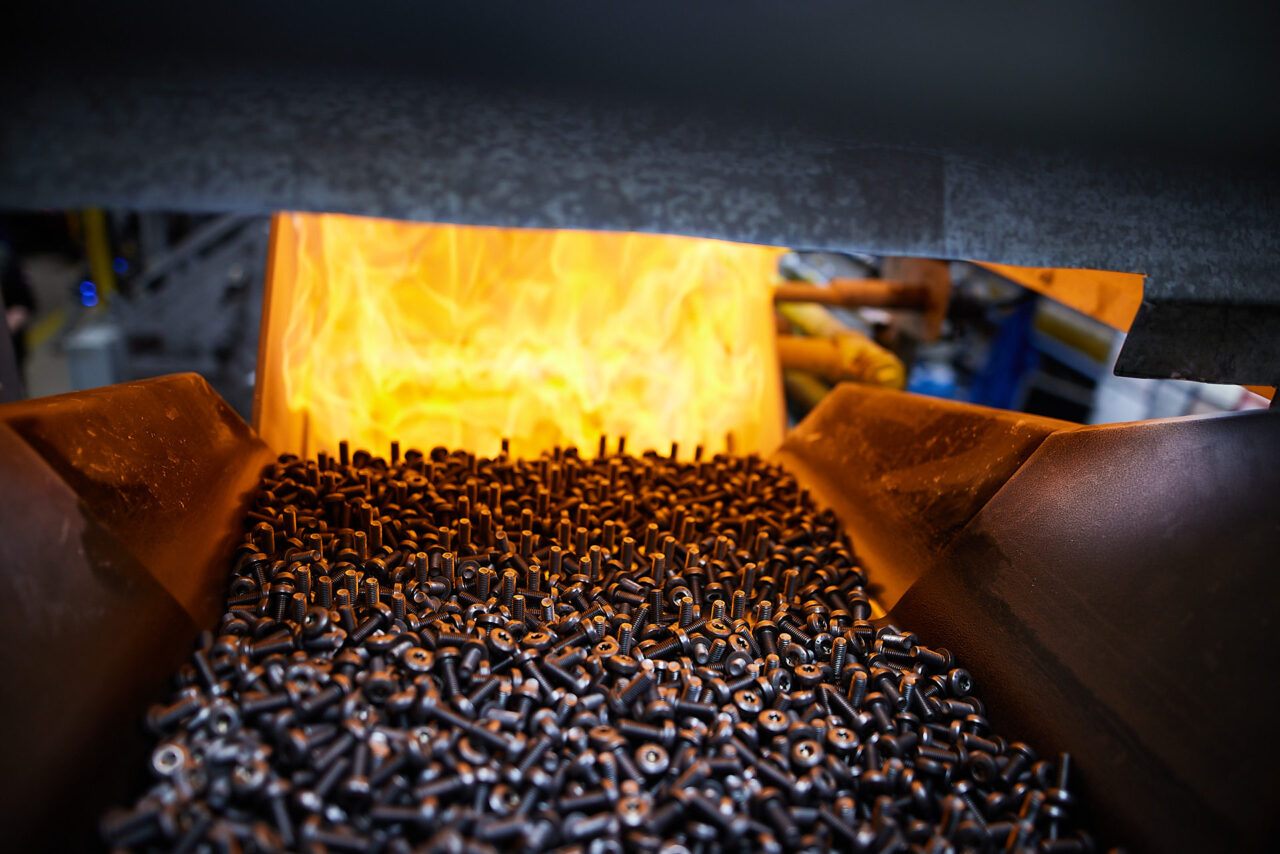
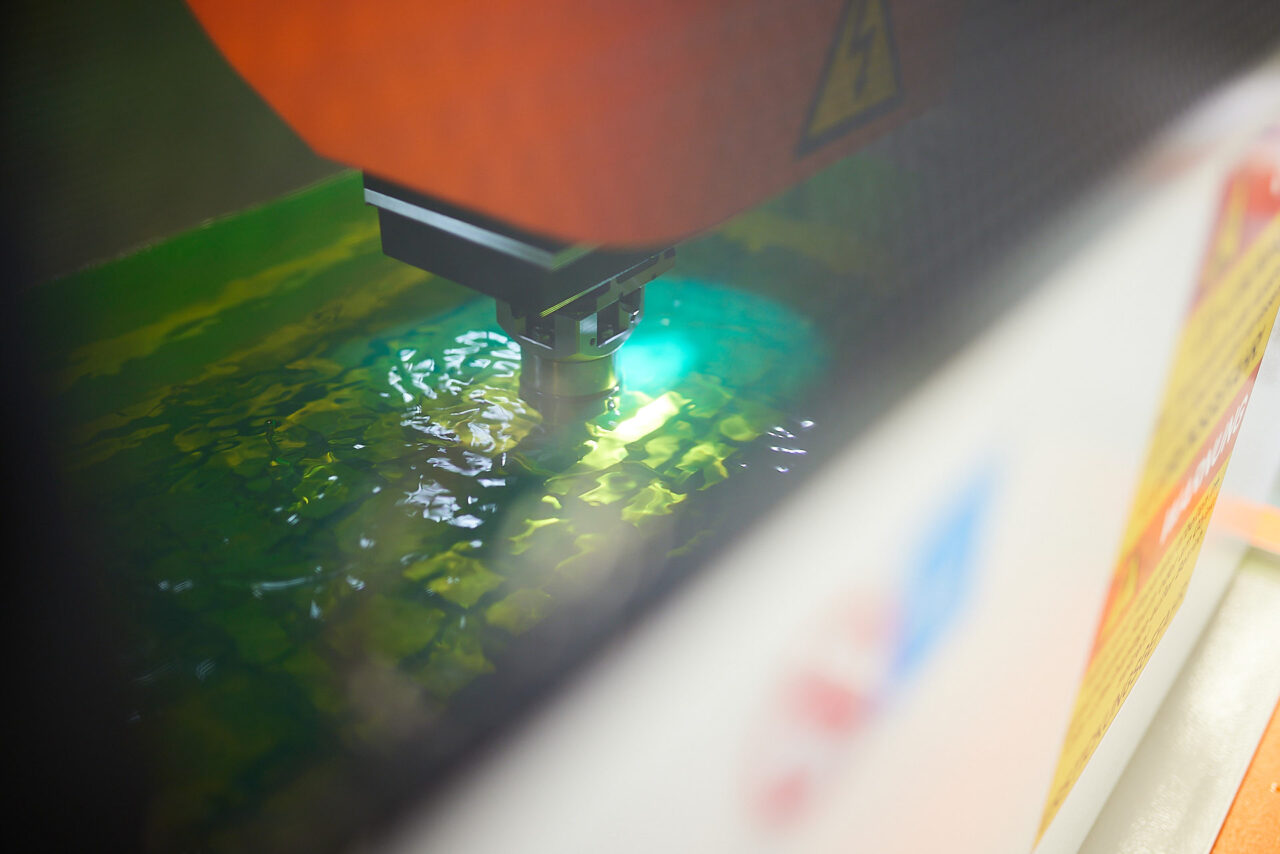
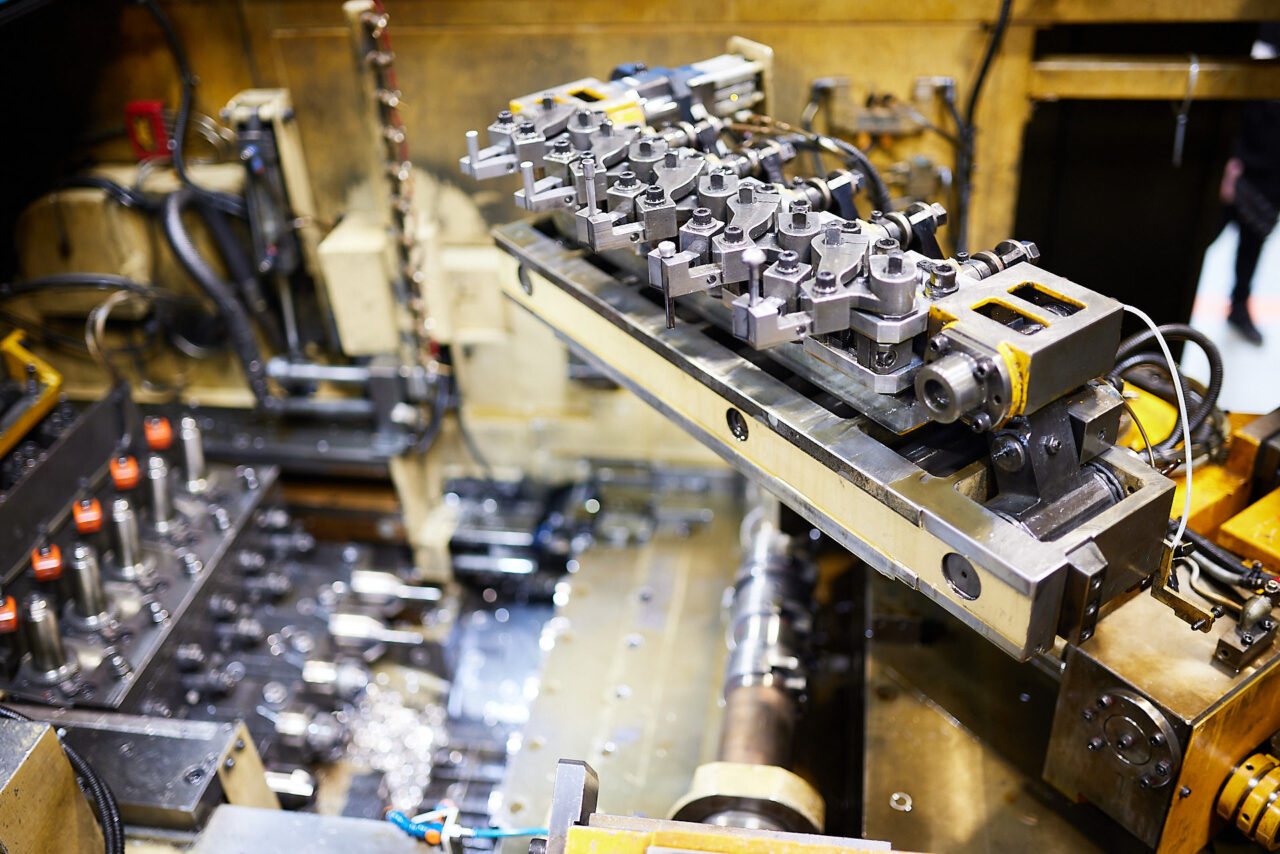
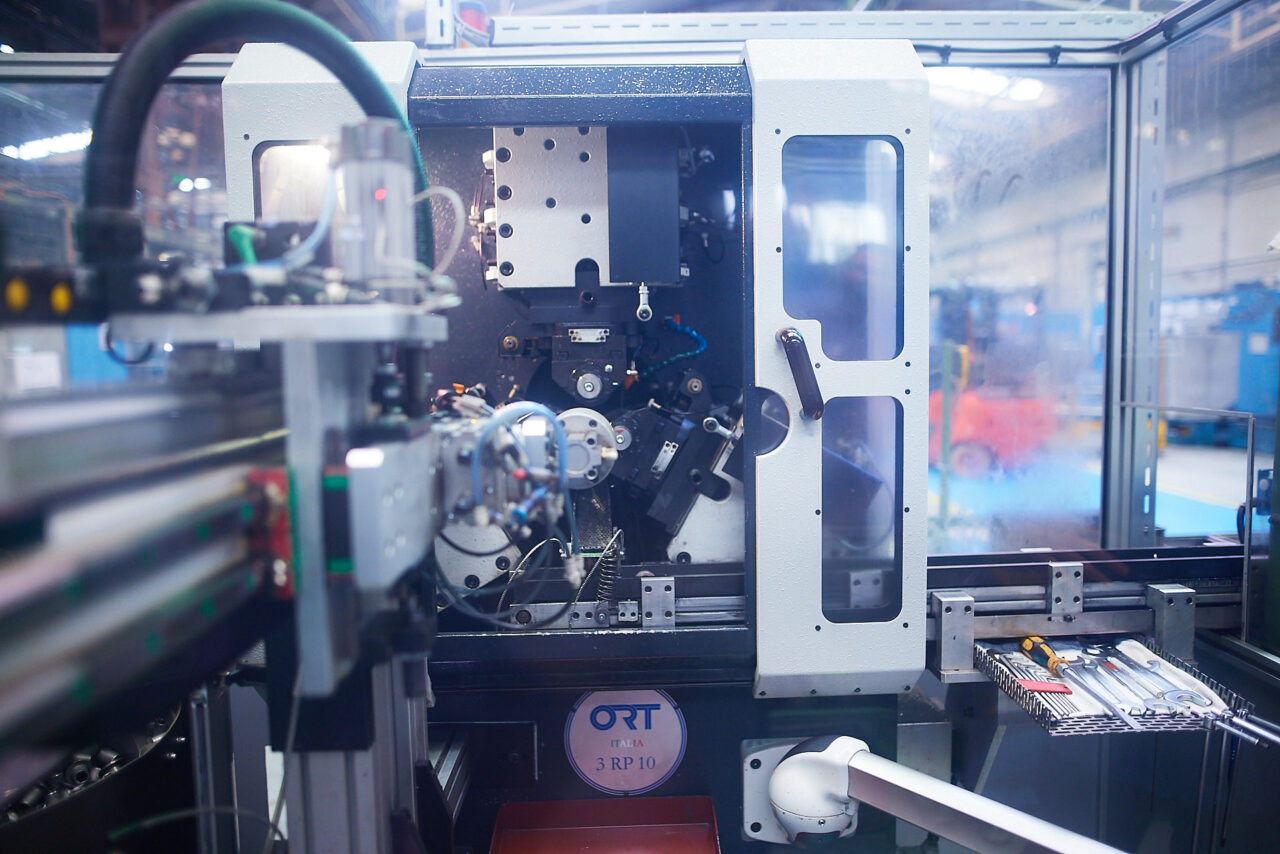
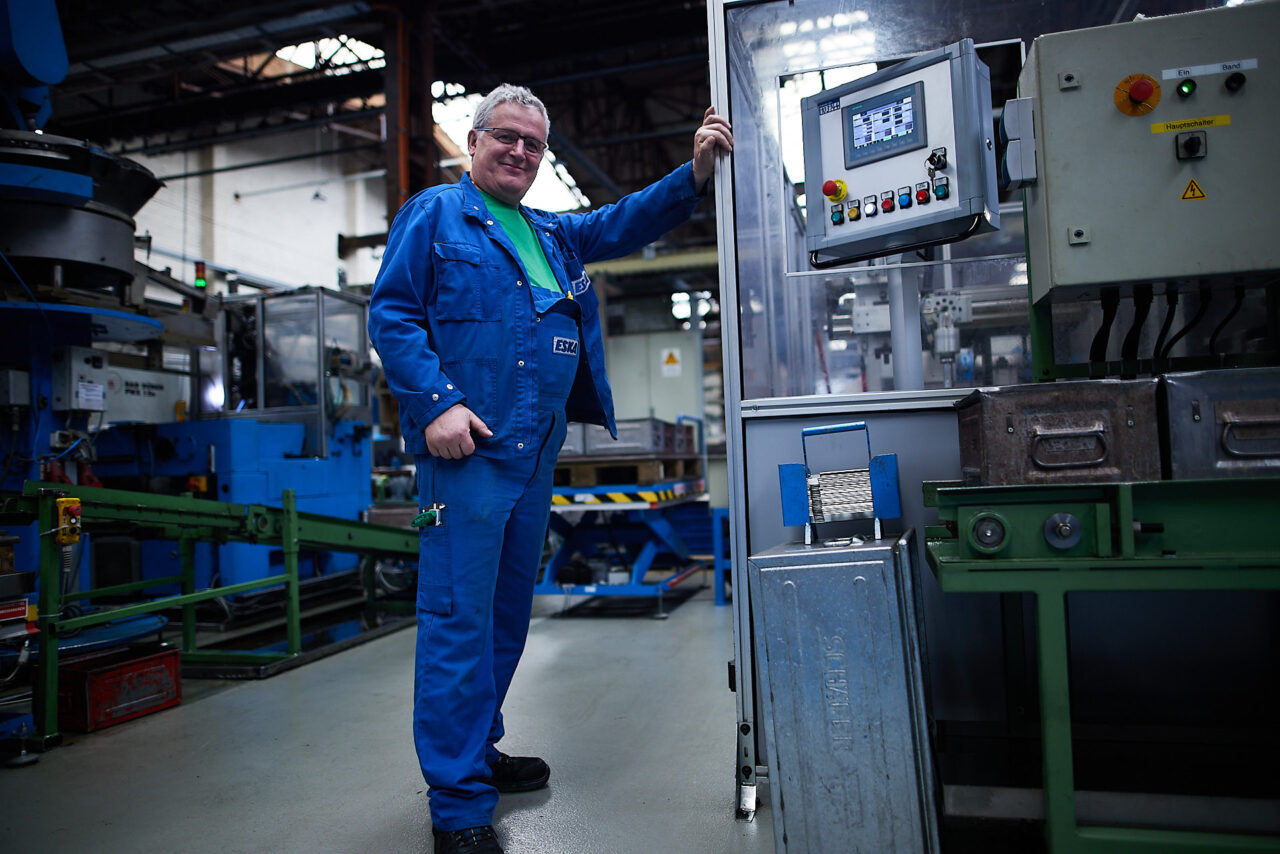
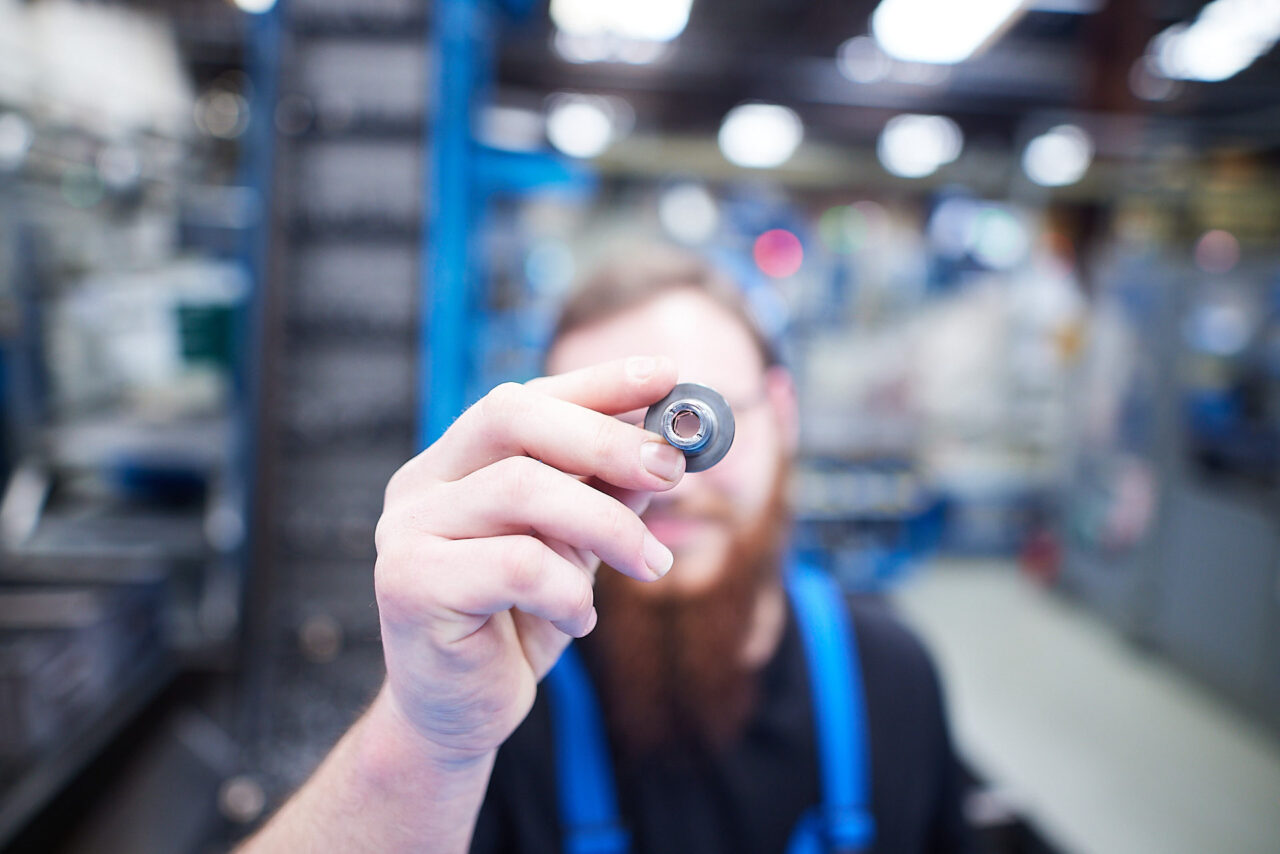
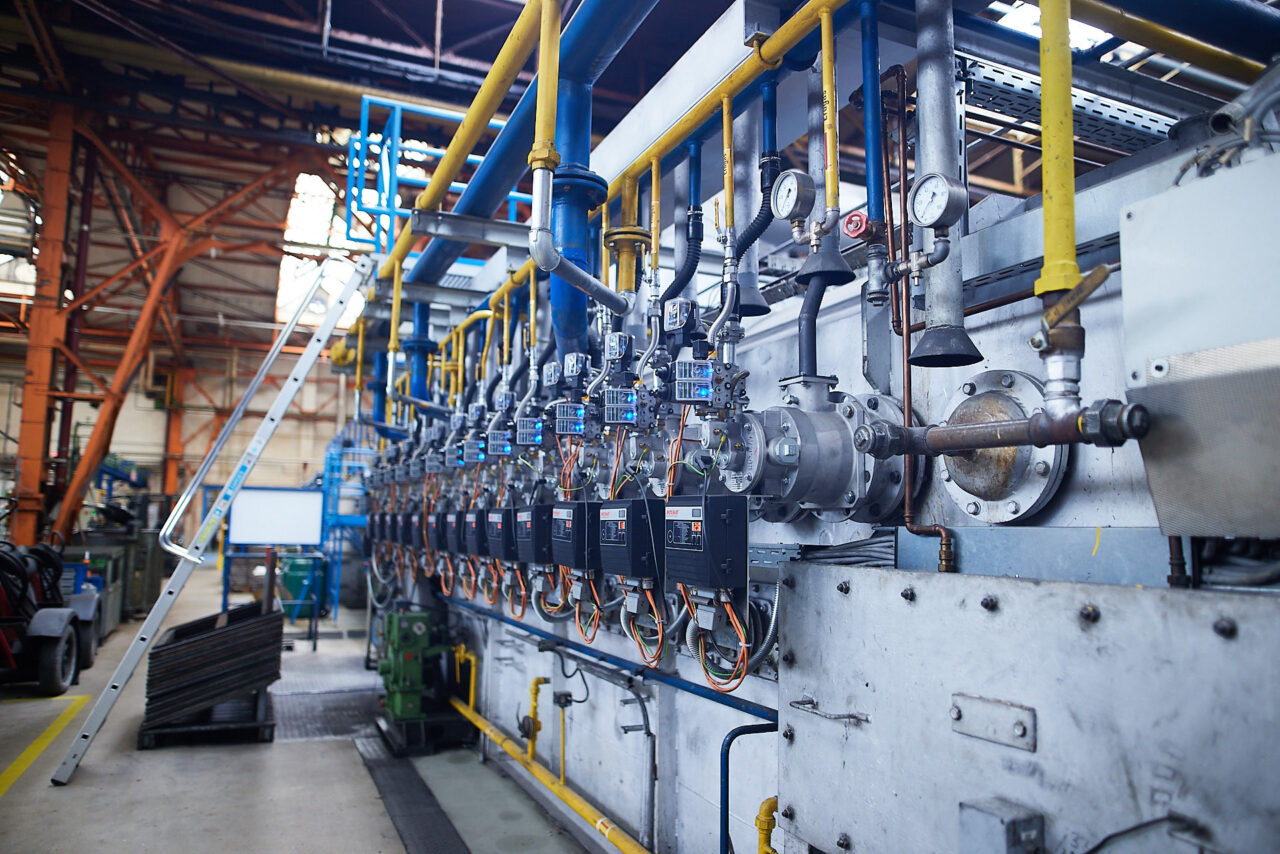
Mechanical post-processing
Process
- turning
- grinding
- rolling
- joining
- drilling
Apart from thread rolling, cold forming on our multi-stage presses often makes further mechanical processing unnecessary. In order to be able to reproduce geometries and tolerances beyond the limits of cold forming, ESKA has the option of mechanically reworking the components.
Highly trained employees operate turning, grinding, rolling, forming and cutting machines, some of which are CNC-controlled, to give the end products the desired shape. Thanks to specially designed production lines and the fully automatic in-house transport system, the products can be fed directly from the pressing shop to further processing. This is efficient, does not involve any special logistical effort and minimizes the risk of mixing parts.
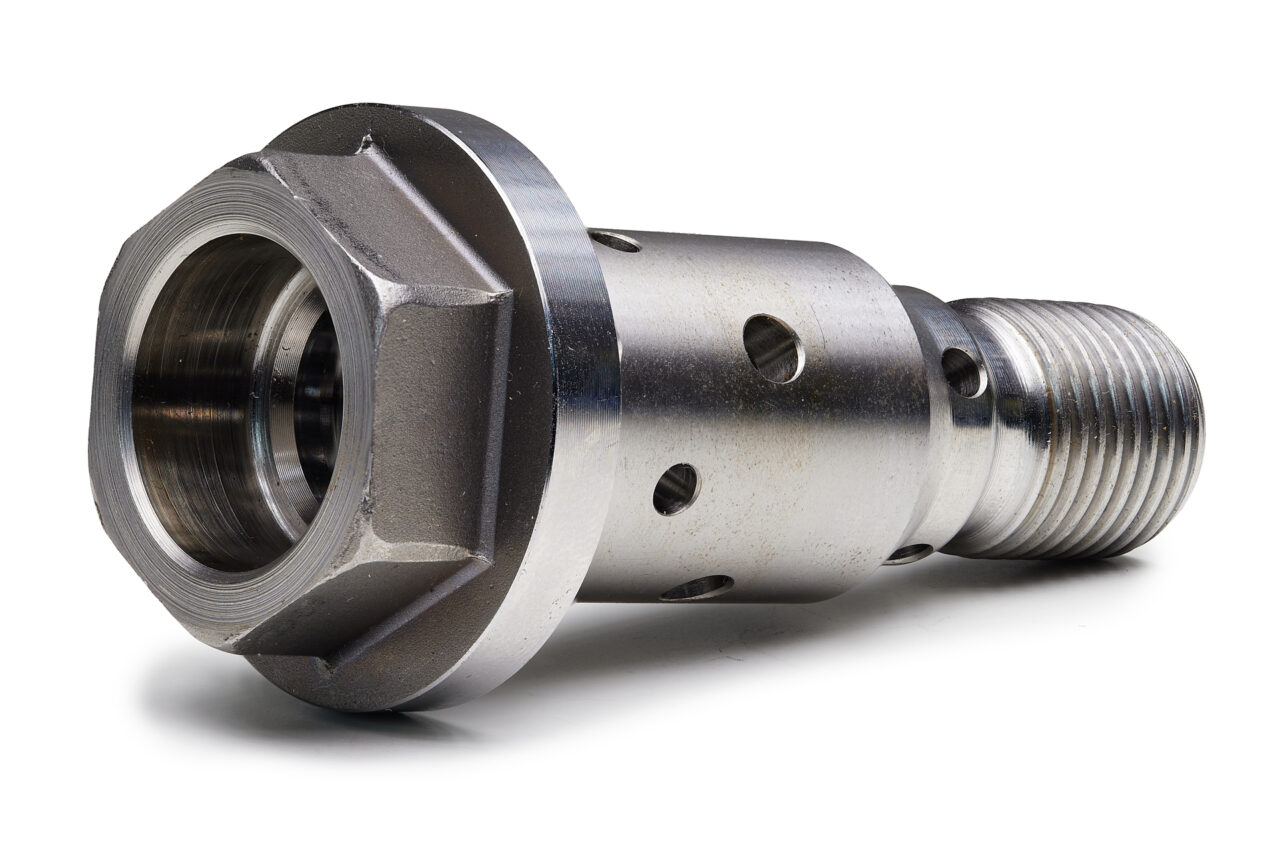
Surface treatment (coating and overmolding)
We can apply all common galvanic and inorganic coating systems in accordance with DIN EN ISO standards and the current OEM standards from qualified suppliers, for example:
- Zn
- ZnNi
- ZnFe
- SnZn
- phosphate coatings (+oiling)
- zinc flake coatings
- electroless nickel
- electroplated nickel
- silver
- Cu-Ni-Sn
- duplex coating (electroplated + org. topcoat)
- and other
Possibilities:
- individual product requirements can be implemented by a large number of suppliers
- adhesive and adhesive coatings in accordance with DIN 267-27 and DIN 267-28
- sealing coatings, also as underhead coating
- retaining rings & mounting aids (Axi-Rad, Plastisol)
- protection against paint and welding splashes or non-stick coatings
- close cooperation with chemical suppliers & contract coaters to enable individual coating requirements
Aluminum coating:
- Lubricant coating to set a defined coefficient of friction
- ESKAlan coating to protect against intergranular corrosion (approval for surface finish x607 in accordance with VW-13750)
- anodizing
- hard anodizing
- electroless nickel
- passivation (e.g. Surtec650 and Alodine 2040)
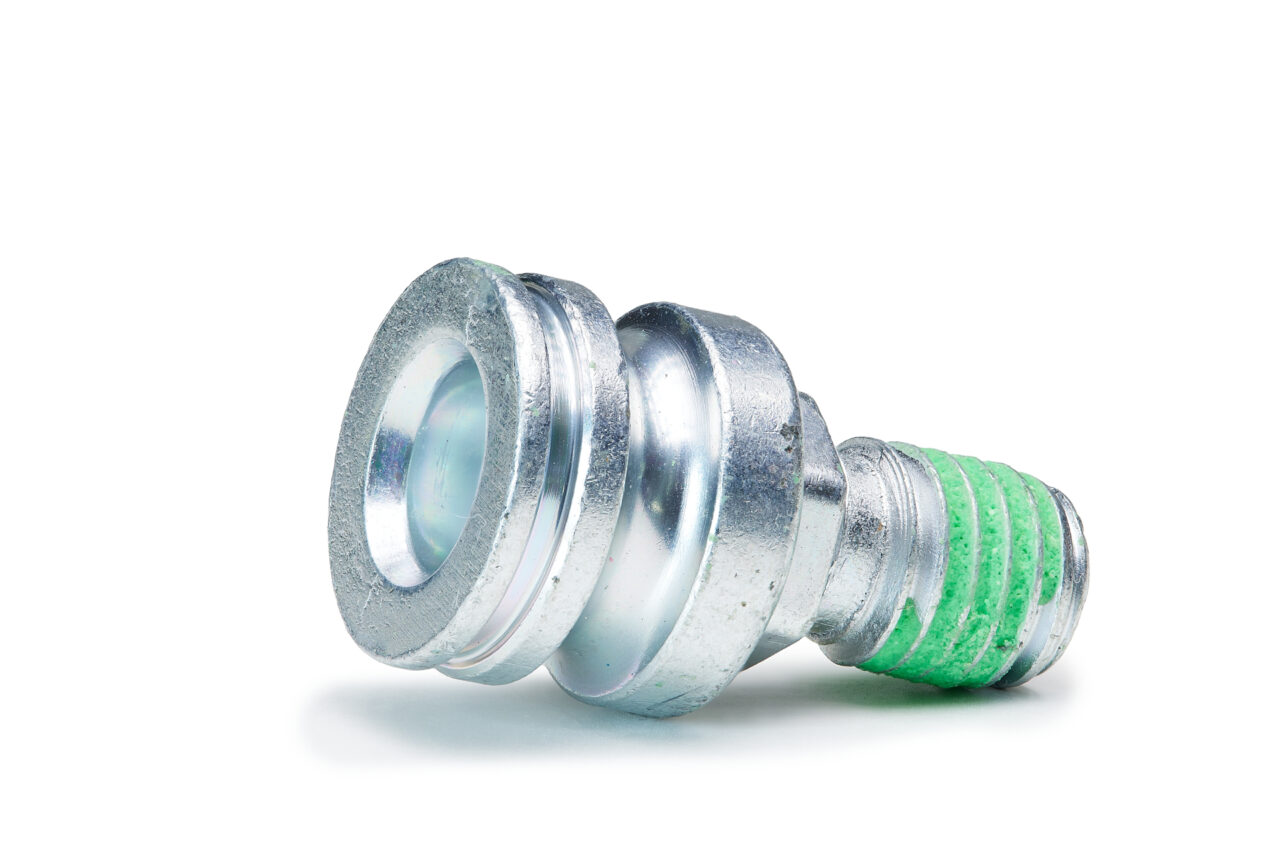
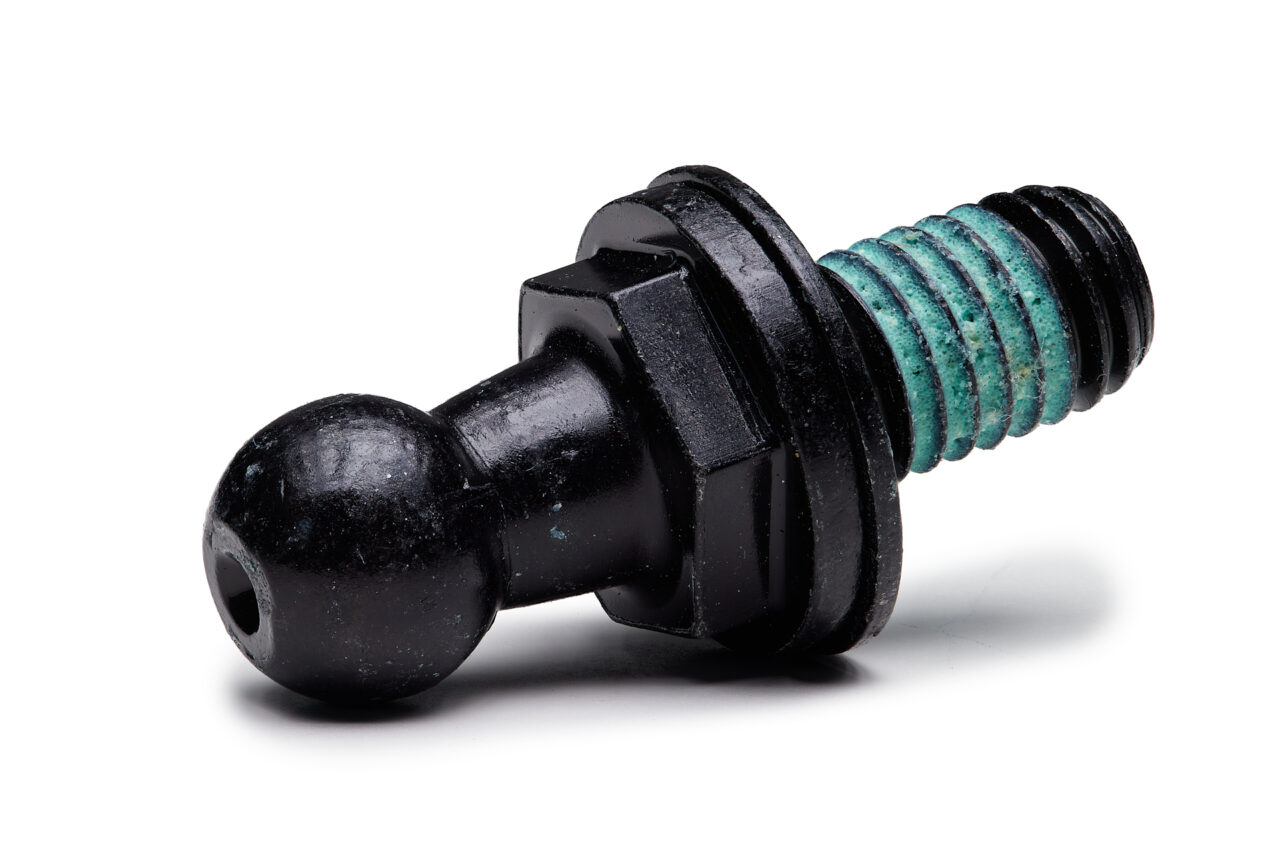
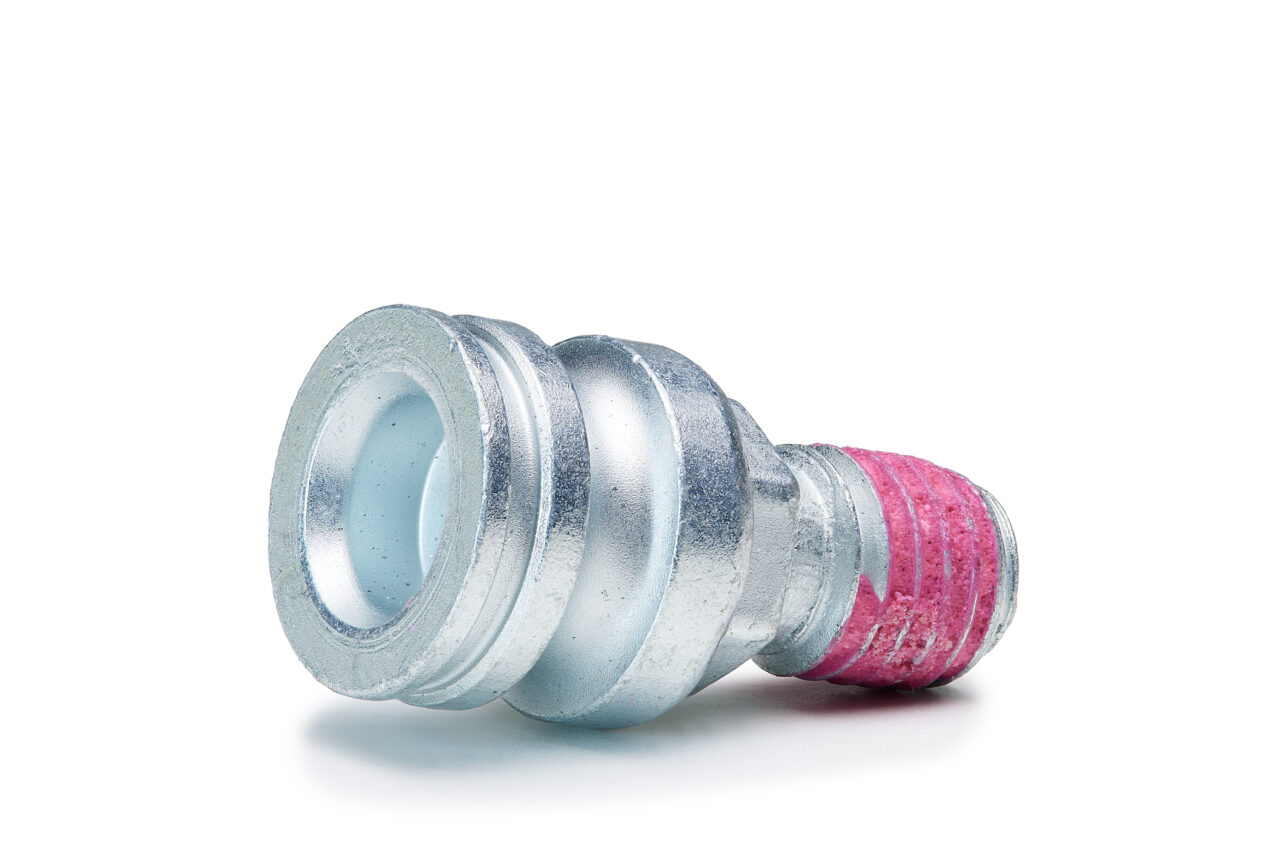
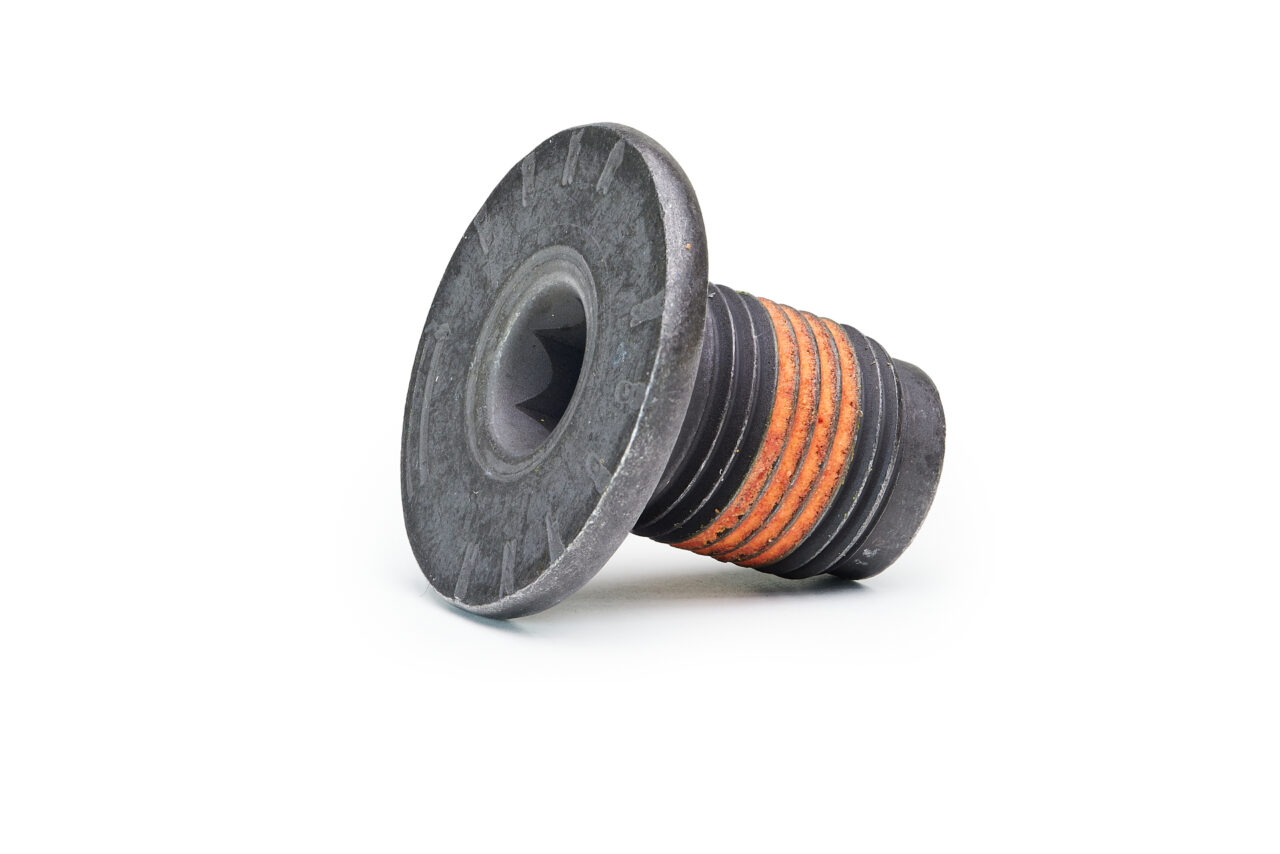
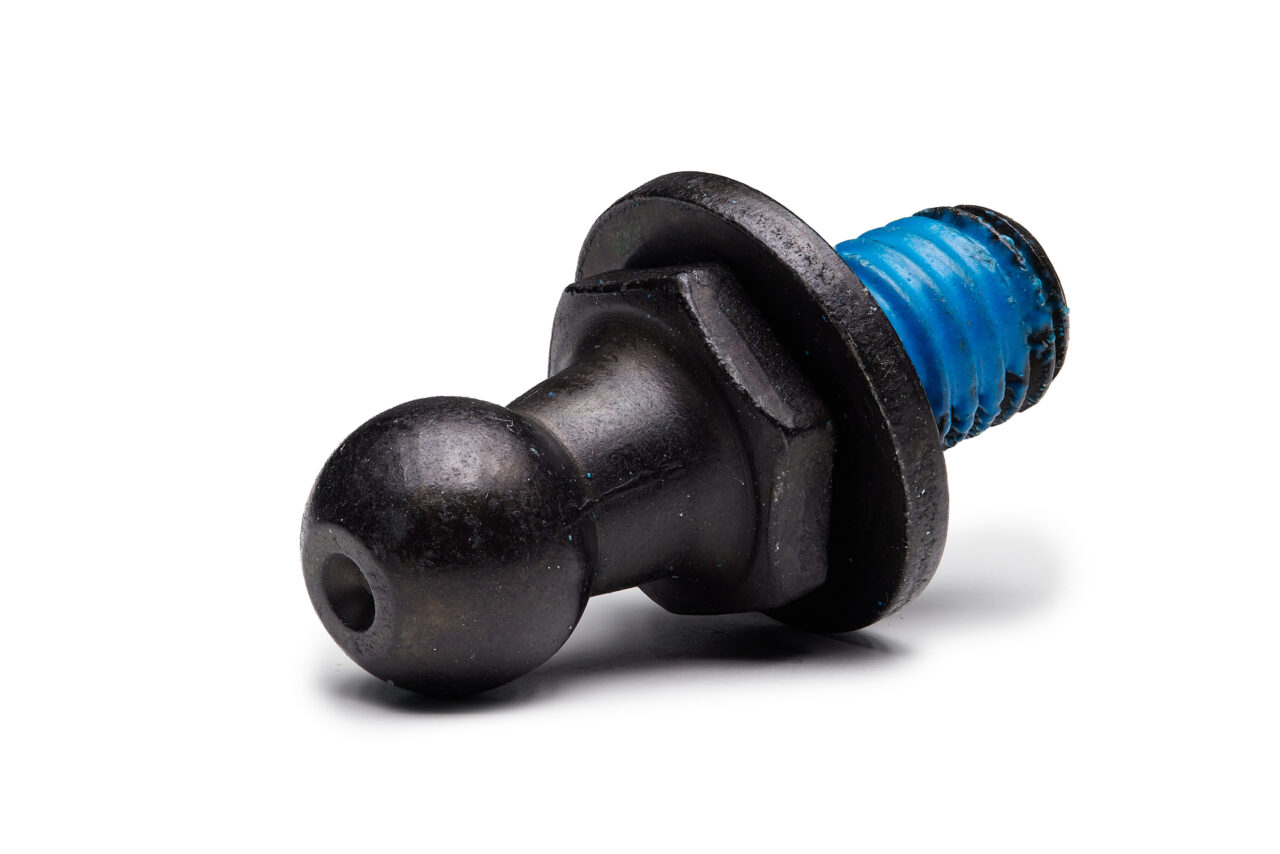
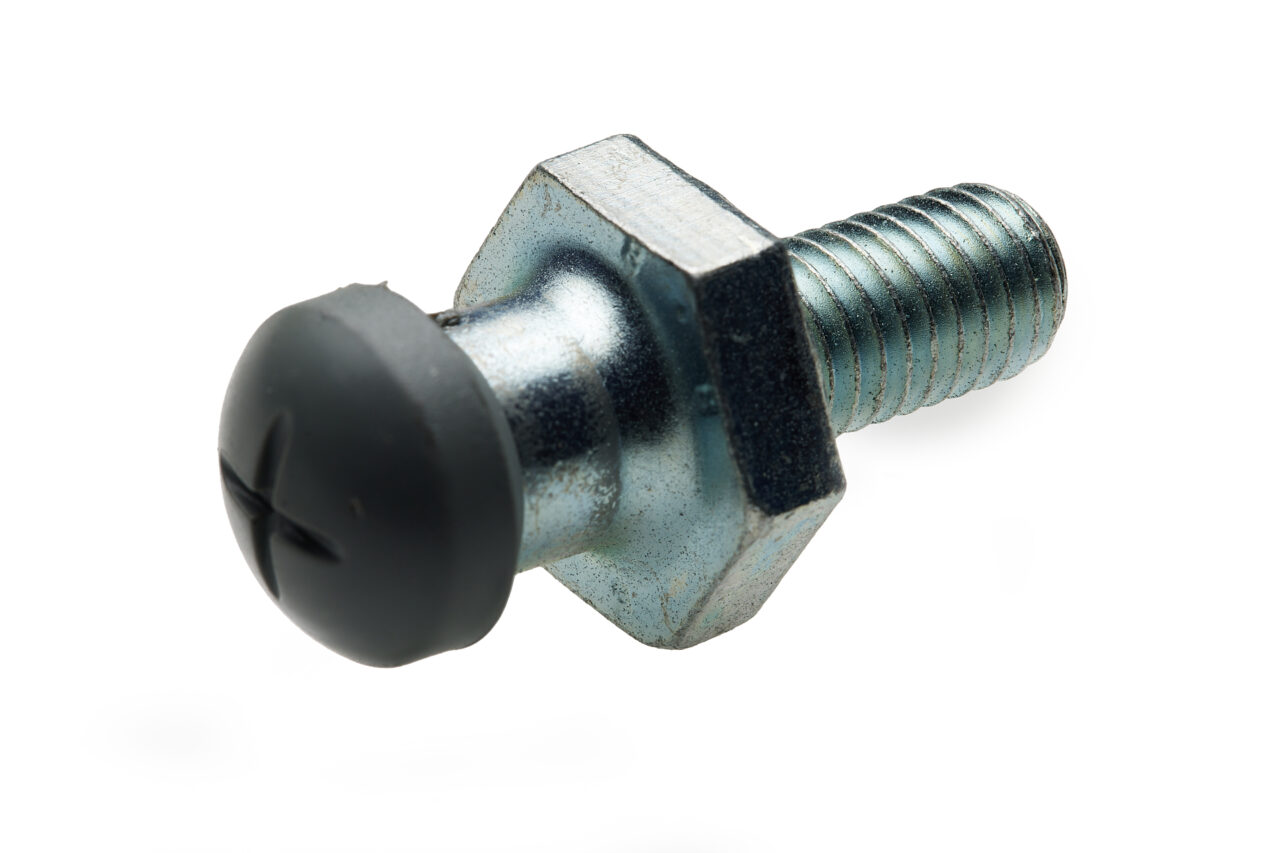
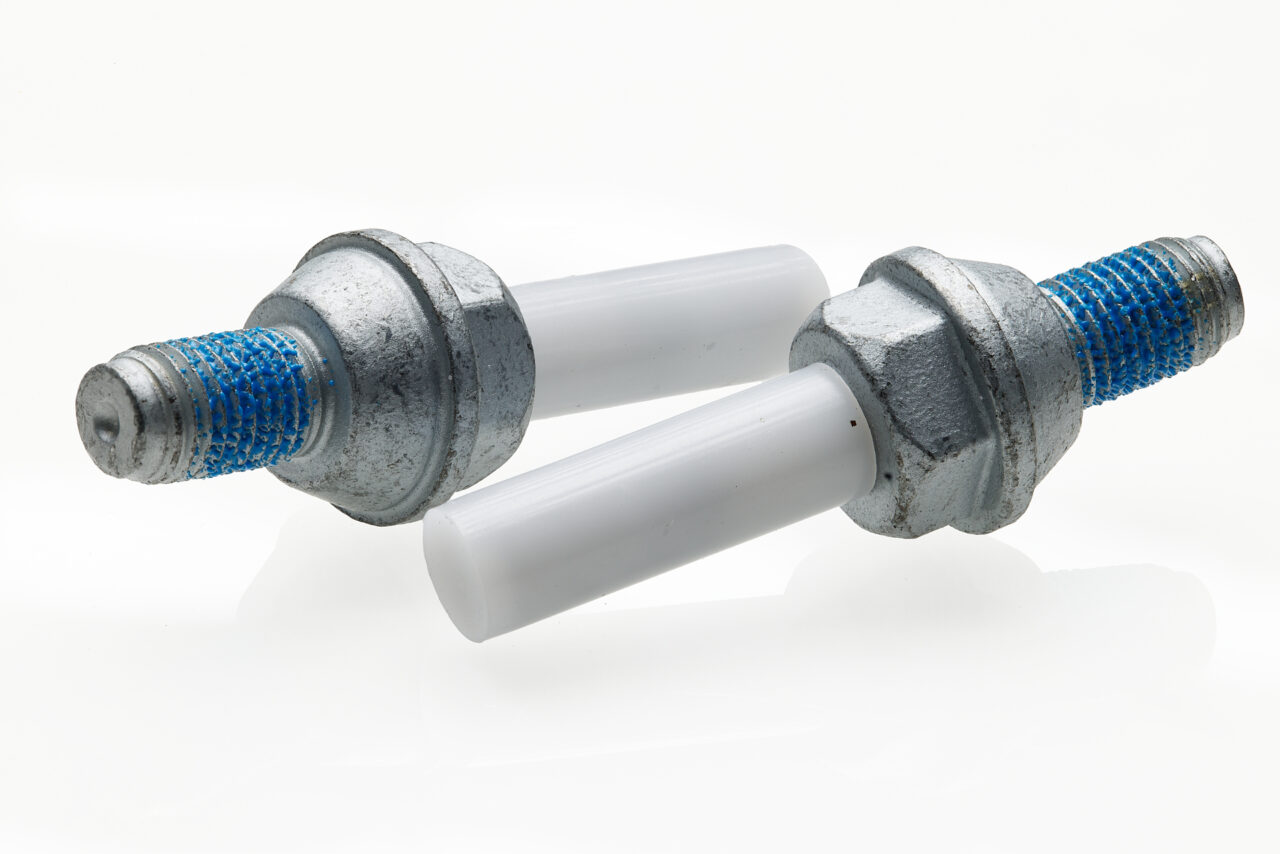
100 % testing
- The products undergo 100% inspection on 22 testing machines
- simple geometries such as thread length, part diameter or more complex requirements such as strength are checked
- in-house realization of customer requirements thanks to a wide range of testing machines
- increased flexibility through investment in modern glass slide testing machine
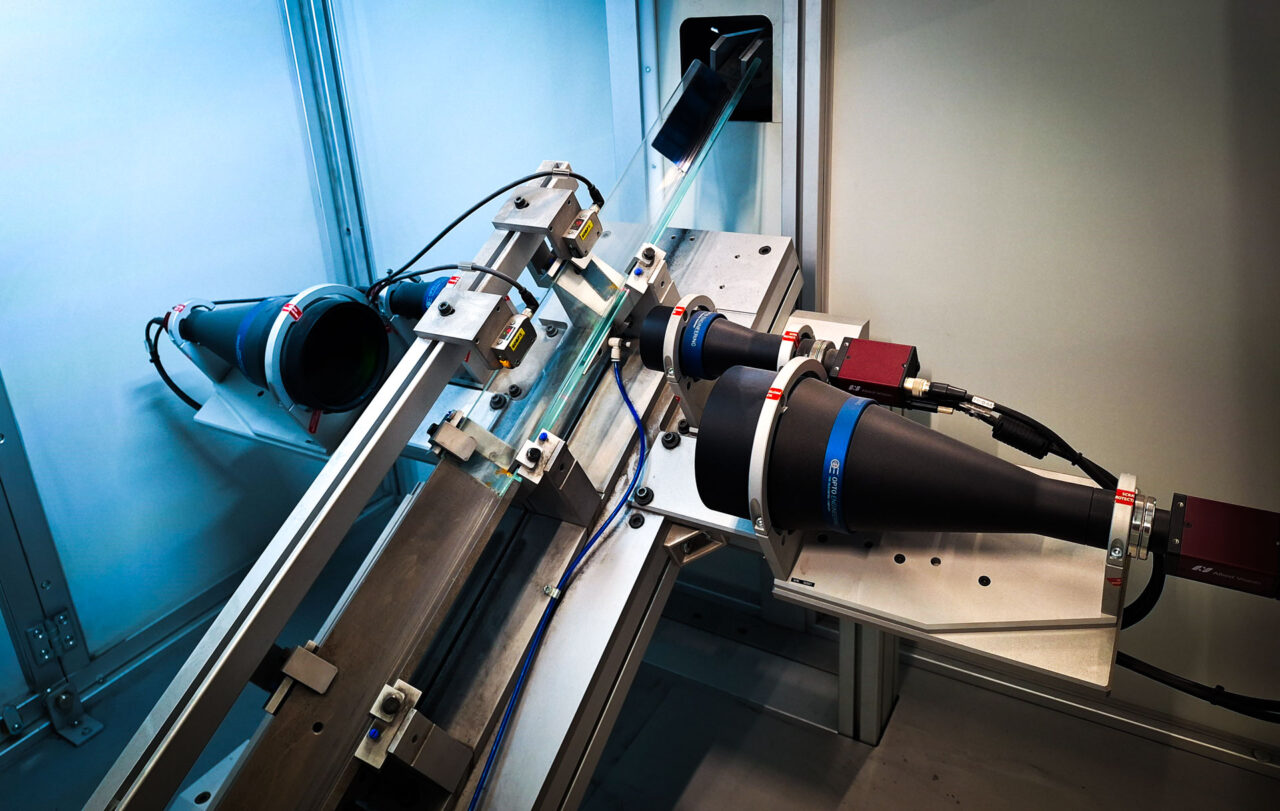

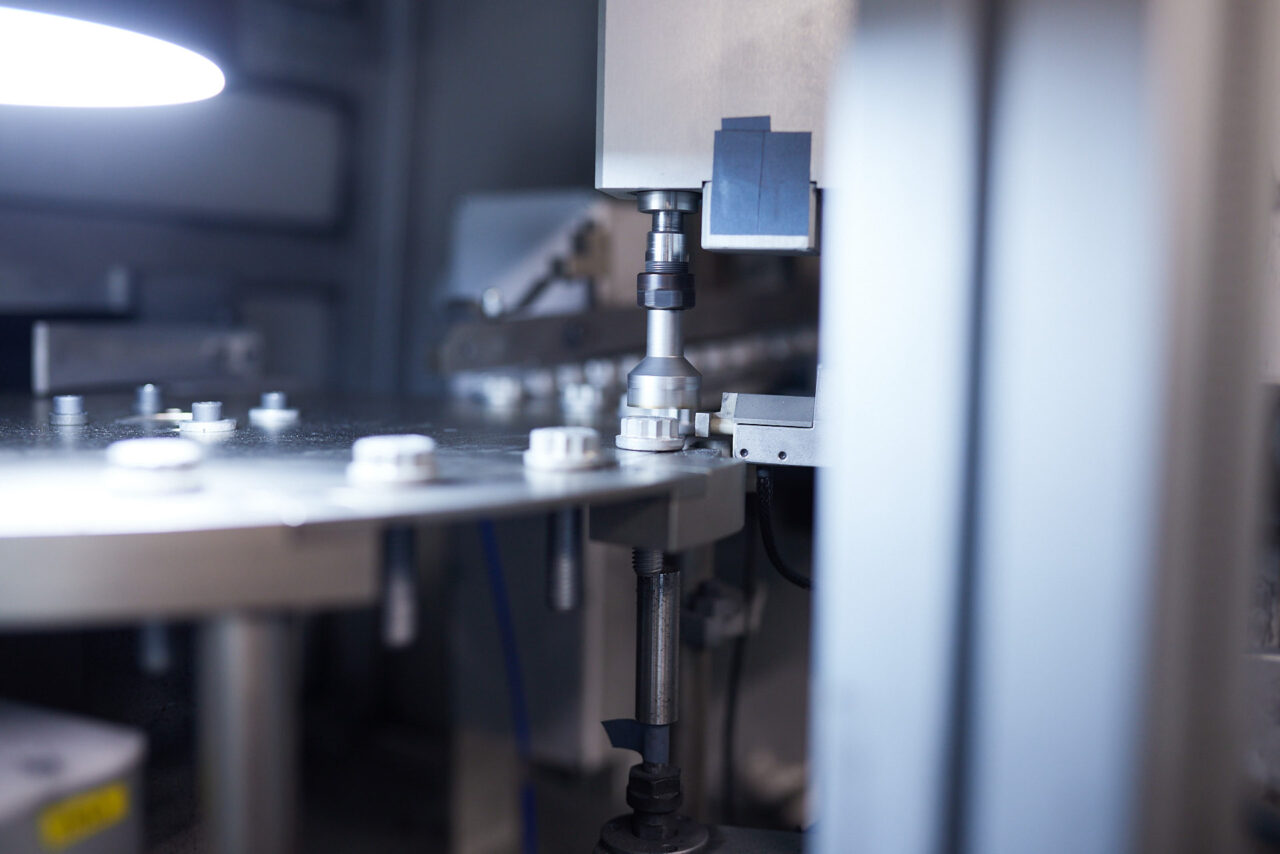
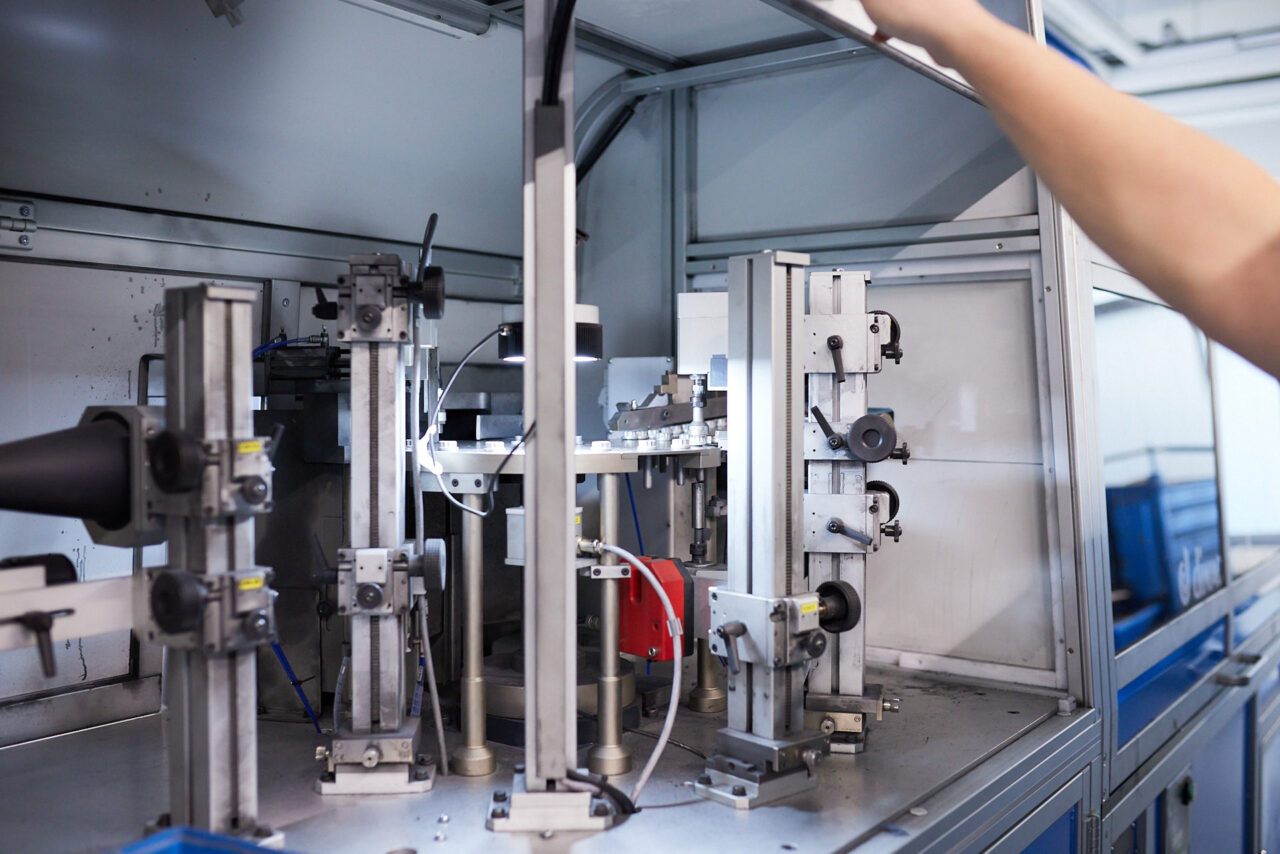
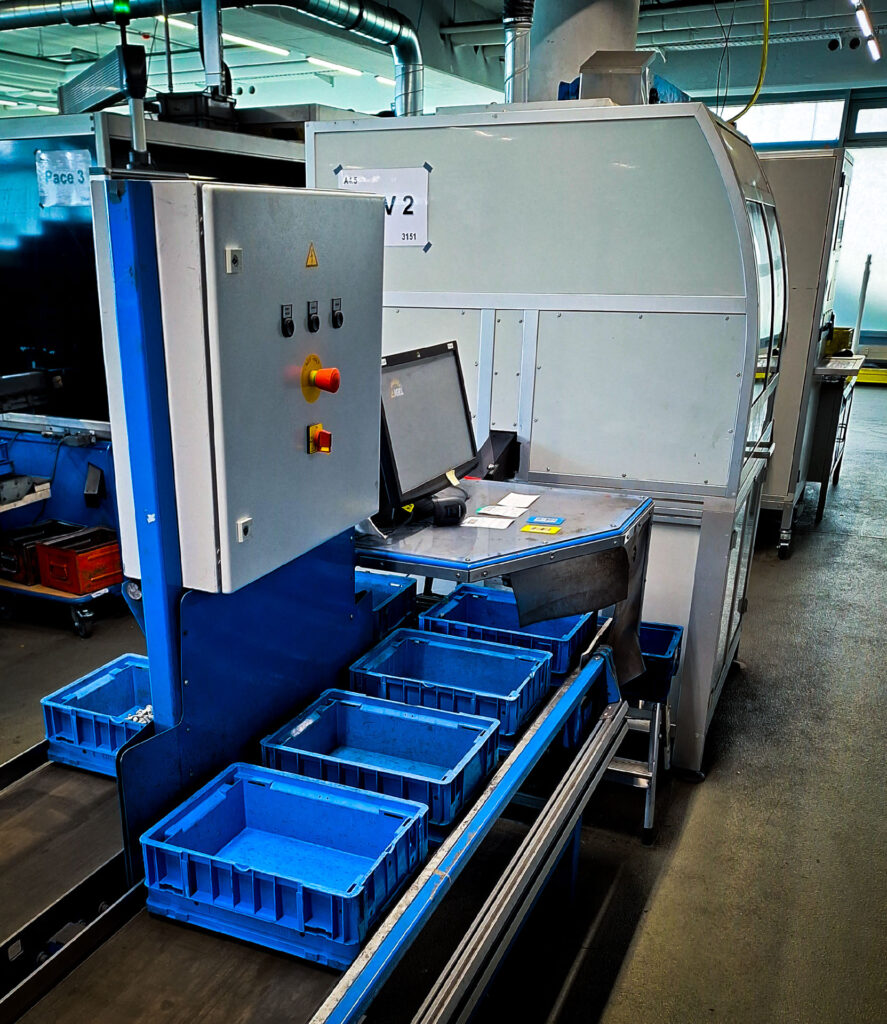
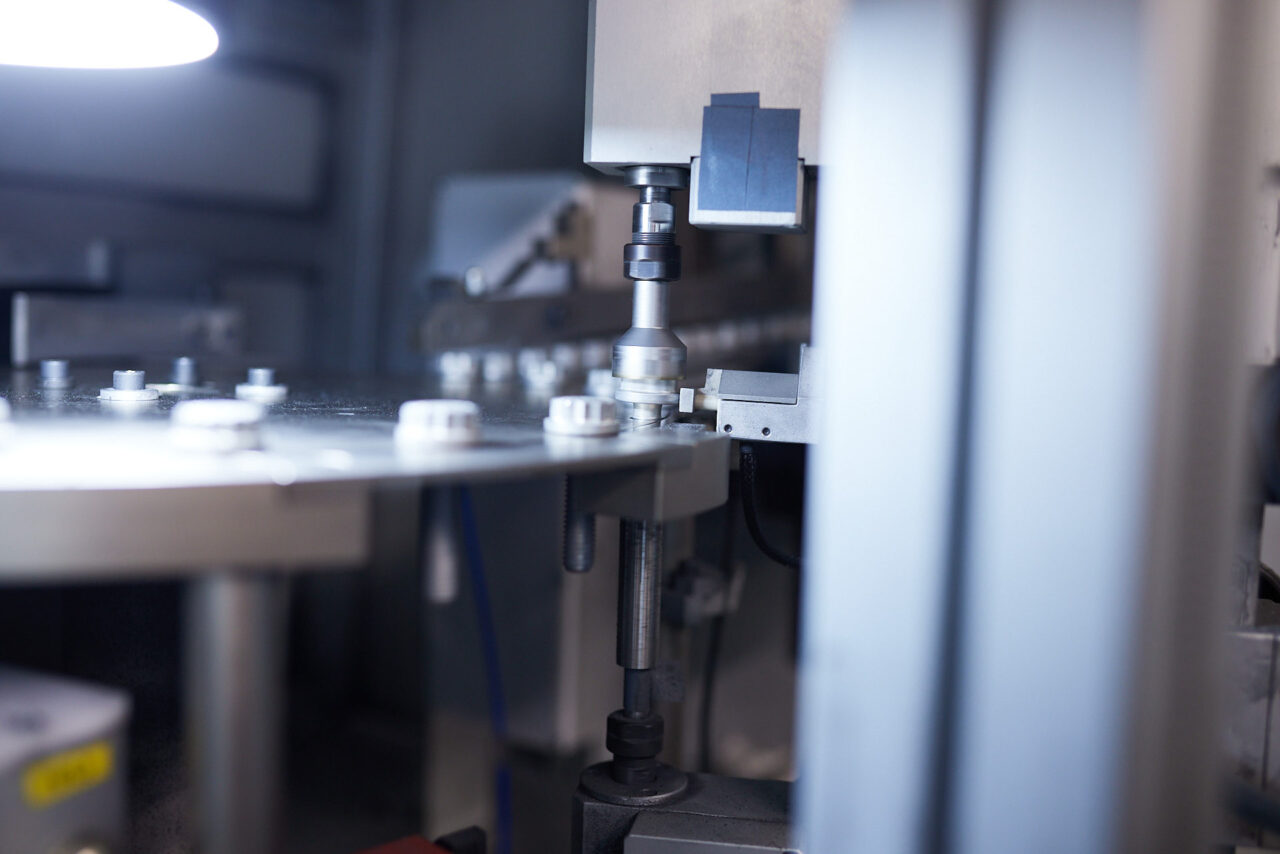